German shipbuilders hold the lead in submarines with electrochemical generators
In States with nuclear submarine shipbuilding technologies, work on air-independent power plants (VNEU) continues to be exclusively export-oriented. This interesting conclusion ends the article of the Deputy Commander-in-Chief of the Navy of the Russian Federation (Navy of the Russian Federation), Vice Admiral Igor Mukhametshin, co-authored with Captain 1st rank Tretyakov. It was published in the latest (6/2023) issue of the magazine "Foreign Military Review" under the heading "Power plants of non-nuclear submarines of foreign countries". Being an experienced submariner, with an eventful service in the North and the Pacific Ocean, Igor Timerbulatovich has held the post of "Head of Shipbuilding, Armament and Armament Operation – Deputy Commander-in-Chief of the Russian Navy for Armament" since 2019. Although the material under his signature does not contain any mention of either Russia or domestic submarines (submarines), the above conclusion is quite suitable for "our case". Indeed, the core of the Russian Navy has been made up of nuclear-powered missile carriers for more than half a century, supplemented by classic diesel-electric submarines (DPL). Note that a similar combination is observed in India (Arihant-type nuclear-powered vessels serve together with the 877EKM, Scorpene and Type 209 diesel-electric submarines). And the PLA Navy, in addition to a pair of submarines-DPL, also has non-nuclear submarines (NPL) of type 041 with VNEU based on Stirling engines (" Foreign contribution to Chinese underwater shipbuilding ", "HBO" dated 04/27.23).
For their part, the United States, Great Britain and France do not build nuclear submarines and submarines for their own fleets, but complete them only with nuclear-powered ships.
WHAT IS GOOD FOR A RUSSIAN IS DEATH FOR A GERMAN
The Russian Russian proverb "What is good for a Russian is death for a German" also reflects the state of affairs in underwater shipbuilding. Following in the logic of the reasoning of Mukhametshin-Tretyakov's article, it is more profitable for Moscow to develop an atomic direction, and for Berlin – a non-atomic one. Only in this way can the Germans retain their leading positions in the international market of underwater equipment while respecting their "non-nuclear" status.
How the Germans broke out into the leaders of the world underwater shipbuilding is described in the article " Germany has stopped producing diesel-electric submarines " ("HBO" from 30.03.23). It is also noted there that, having refused to further improve the classic DPL, the company TKMS (abbreviation ThyssenKrupp Marine Systems, this is the marine division of the industrial giant ThyssenKrupp) by now It has completely switched to the construction of NAPS with electrochemical generators (ECG). They work on hydrogen stored on board in the form of intermetallic compounds. The electric power generation system is built on fuel cells. It is designed and manufactured by Siemens.
The NAPL family consisting of two main projects went into a large series. Type 212A boats are designed for the German and Italian fleets. And purely export Type 214 submarines were supplied to a wide range of foreign customers and are currently being built under license at shipbuilding enterprises of partner countries (" Koreans plunged into the underwater theme ", NWO from 06/22/2023 and " Turkey will develop a submarine itself", NWO from 06/04/2023).
The boats of the family were developed by Howaldswerke-Deutsche Werft (HDW), currently part of the industrial giant ThyssenKrupp (or rather, its marine branch TKMS). The release of design and working documentation was carried out with the involvement of the ILK Design Lubeck design bureau.
Traditionally, the German way in military shipbuilding is characterized by the high complexity of engineering solutions, as well as the high cost of final products in pilot and serial production. This is especially evident in the line of the ship's power plant, including its maintenance during operation. All this is reflected in the Type 212A boats. Therefore, a number of countries around the world considered and eventually refused to purchase the latest German NAPS in favor of the German, but classic Type 209 diesel-electric submarines of the previous generation.
PROJECT FEATURES
Germany started research works on the topic of hydrogen production on board submarines at the end of the last century. Several experimental installations were tested in laboratory conditions at the turn of the century. Then their comparative analysis was carried out.
Based on the results obtained, it was decided to store hydrogen fuel for the anaerobic power plant NPL in the form of intermetallic compounds. This decision is indisputable. The inconvenience of storing hydrogen on board the ship in the form of intermetallic compounds, as well as the inertia of the fuel system of the VNEU and large storage volumes are noted.
As a result, Type 212A submarines turned out to be three times larger than those they replaced in the German Navy, namely Type 206.
However, the advantages offered by the VNEU forced naval commanders to come to terms with these and other disadvantages of boats with an anaerobic system. The German designers themselves believed and were able to convince the admirals that the German technical genius was able to create a fairly compact and at the same time relatively cheap energy system for swimming underwater.
As a result, this led to the development of a submarine, which received the designation Type 212A. The suffix "A" indicates the so-called second batch, since this project was preceded by the development of a classic-looking submarine (DPL). It was also not in vain – Germany built several boats of classic design for the Israeli Navy. We are talking about the Type 800 – an export submarine built in triplicate: Dolphin, Leviathan and Tekumah. At the end of the last century, they were assembled at the shipyard in Kiel and handed over to Israel in 1999-2000.
The hallmark of modern German submarines is a single multimode alternating current electric motor on permanent magnets of the Siemens Permasyn type, as well as VNEU on Siemens fuel cells, hydrogen for which is stored in an intermetallic way.
Production of the first batch of four submarines for the German Navy began at the end of the last century, with delivery in 2005-2007.
It turns out that the process of developing and bringing to mind the German type of anaerobic power plant took a very long time. From the beginning of work on the experimental machine to the adoption by the fleet of the first Type 212A submarine, 25 years have passed.
In 2007-2008, an additional pair of similar submarines was built with delivery in 2015-2016. According to TKMS, the lead boat was built for seven years, the last pair of serial ones – eight, at the peak of production, the production cycle was reduced to five years.
Thanks to its advanced power plant, the Type 212A can spend up to three weeks underwater. In particular, during the tests, the U-32 submarine traveled 1,500 miles in two weeks without surfacing. Thus, the compliance of the project with the technical task of the German Navy in terms of underwater autonomy was demonstrated.
EUROPEAN PARTNERS AND SPONSORS
The anaerobic power plant for Type 212A submarines was created primarily to meet the needs of the German Navy, but with the expectation that it could also be used on export-looking boats.
In addition to six boats for the German Navy, several more were built for Italy. This country refused to continue its own line of diesel-electric submarines in favor of producing submarines under a German license. In the new century, the government in Rome decided to cooperate with Berlin in the construction of the local shipyard Cantieri del Muggiano. The topic is handled by Fincantieri. Four boats were commissioned – with delivery in 2006, 2007, 2016 and 2017. The production cycle ranged from five to seven years.
Negotiations are underway between Berlin and Rome to continue the series. It is planned to build four more boats with delivery from 2027 to 2033. Most likely they will be made according to a new project, which means that the Type 212A series will not go beyond the already built 10 buildings.
Let's pay tribute to German scientists, designers and technologists. They managed to create a submarine with an almost "absolute" anaerobic power plant, which is characterized by low noise, low operating temperatures, with the discharge of ordinary water into the sea. This achievement was made possible thanks to long-term research, which was partially funded from the state budget, as well as pan-European green energy programs.
The success of the Type 212A submarine program would not have been possible without strong state support, including through the United Europe. Within the EU, programs have been underway for a long time to introduce hydrogen energy into various areas of industrial development, including the automotive industry. Uninterrupted operation of the new type of submarines has become possible thanks to large investments in coastal infrastructure. In addition, the reorganization of the previously created personnel training system was required. After all, it is difficult to ensure trouble-free operation of new submarines without extensive knowledge and automated actions of the crew.
EXPORT OPTION
Along with the obvious advantages, the Type 212A is not without drawbacks. One of them is considered to be weak armament: anti-ship missiles are not provided, and the number of 533-mm torpedo tubes is limited to six (with 13 units of ammunition).
The designers tried to eliminate this and other shortcomings on the export version of the boat, which received its own designation – Type 214.
On the one hand, its design and body saturation have been somewhat simplified. On the other hand, the designers decided to go for a slight increase in displacement in order to correct a number of points that turned out to be erroneous on the basic Type 212A or did not fully justify themselves.
So, the Type 214 received eight torpedo tubes – a couple more than the original Type 212A project. For this, as well as more comfortable conditions for the crew, the total length of the product has been increased by 9 meters, to 65. The surface displacement increased by 240 tons, to 1,690, and the number of crew remained at the level of 27 sailors and officers.
Instead of high-strength German low-magnetic steel, the case is made of American HY100. This alloy is cheaper and more common, since it was used to make the hulls of serial nuclear-powered submarines for the US Navy.
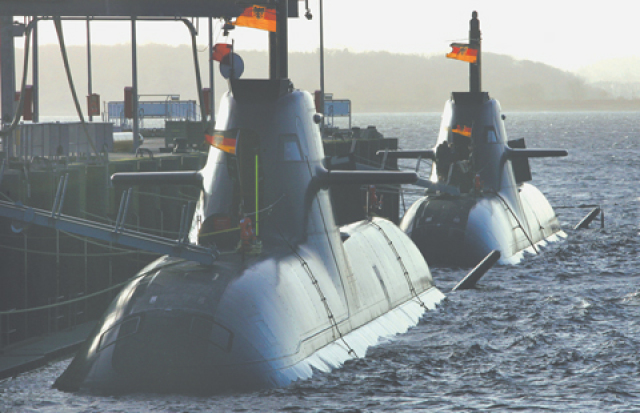
The re-equipment of the underwater component of the German Navy required major investments in the infrastructure for the production and storage of hydrogen fuel. Photo by Reuters
Collectively, the total number of active Type 214 submarines currently stands at 15 units. Of these, only three were completely made in Germany in 2010-2011: one was transferred to Greece, the remaining pair went to Portugal.
The needs of Germany's own naval forces are relatively small, and they alone do not cover the costs of R&D, production preparation and the cost of building serial samples. Numerous foreign orders help to maintain the high load of German underwater shipbuilding. At the same time, Berlin willingly distributes licenses for the production of non-nuclear submarines according to the projects of German designers. Type 212A submarines are assembled in Italy, Type 214 – Turkey, Greece, South Korea.
Compared with direct deliveries, license trading, of course, reduces the total revenue. But the German government and industry have found solutions that make it possible to engage in military-technical cooperation with benefits. Relations with foreign clients are built in such a way that the most high-tech components of the hull saturation of submarines are produced only by German companies. Work that does not bring a large margin and does not require high-tech production is given to the side.
The manufacture of hull parts, the assembly of the boat, the laying of communications can be carried out without using high technology. The Germans completely reserve the release of the power plant, sensors and electronic equipment, partly – mine-torpedo weapons. It is in these areas that the main investments in R&D are made, so as to maintain and increase the scientific and technological gap from partner countries and competitor countries in the underwater equipment market.
As for the licensed release of Type 214, Greece became one of the countries that mastered it. Three ships were assembled there, they entered service in 2015-2016. Taking into account one German-built hull, the Greek navy has four Type 214 boats.
The Republic of Korea has attracted two companies – Hyundai and Daewoo – to carry out the licensed assembly program. The beginning of the project dates back to 2002. In total, from 2007 to 2020, South Korean sailors accepted nine boats of the German project with an anaerobic power plant from the local industry.
In 2011, Turkey signed an agreement with ThyssenKrupp for the licensed production of six Type 214 ships. The main hull was launched in 2019. Currently, the boat is being tested and has not yet been introduced into the permanent readiness forces.
As of spring 2023, the number of active boats of projects 212A/214 is 25 units. It is also necessary to take into account three more boats operated by Israeli submariners – Tanin, Rahav and Drakon. This trio was built at the shipyard in Kiel and transferred to the customer from 2014 to 2022. Tanin practically does not differ from Type 212A, including VNEU, although it passes as a modification of the classic Type 800 DPL. The estimated cost is $700 million per unit of production, part of it is paid by the German government.
Together with the three Israeli boats, the total number of boats of the family built on the basis of Type 212A is 28 units. All of them were transferred to customers in the XXI century. Of this number, 12 were built in Germany (six Type 212A, three Type 214 and three Tanin).
METAL HYDRIDE ALLOY
Modern German submarines with VNEU are very complex products, their uninterrupted operation requires a special infrastructure in the home port (for hydrogen production, storage and refueling).
Large labor costs were also needed in the development of the topic of fuel cells as such. The Siemens concern took the leading role here. Fuel cells as a product are characterized by complexity: it is necessary to solve the problem of hydrogen storage. Hydrogen metal hydride used in Type 212A and Type 214 submarines makes it possible to achieve a high level of safety. At the same time, however, the hydrogen storage system turns out to be quite cumbersome.
Here, the German designers had to make a number of compromise solutions, since it was necessary to find a balance between efficiency and safety. In general, this topic has always been and remains relevant in the development of underwater technology. In this case, it was necessary to find acceptable solutions between the mass of the metal hydride alloy (it turns out to be quite large) and the low content of hydrogen in it. An increase in the amount of hydrogen leads to an unacceptable value of the mass of the storage system in terms of the dimension of the submarine.
There was and remains skepticism about the applicability of the German metal hydride alloy storage system in the case of a submarine whose operation is carried out in climatic areas with elevated seawater temperatures. A characteristic feature of a metal hydride alloy is the release of hydrogen just when the temperature of the alloy increases. Accordingly, when operating in tropical conditions, it can be expected that a negative effect will be observed if the release of hydrogen begins involuntarily.
The German Navy initially expected to limit the area of operation of the new submarines to the waters of the Baltic and the North Sea, where the seawater is quite cold. Based on the expected operating conditions, the topic of involuntary release of hydrogen was not relevant. It was with this in mind that the designers chose the parameters of the Type 212A submarine.
The need for some kind of correction arose when Italy decided to join the program. However, the analysis showed that the operating conditions in the northern Mediterranean are quite acceptable, and therefore significant changes were not required then. Discussing the topic of the operation of German and Italian submarines, it must be remembered that both in the Baltic and off the northern, western and southern coasts of Europe, NATO submariners operate in areas confidently controlled by aircraft and ground assets of the armed forces of the North Atlantic Treaty. Therefore, the entry into the sea and the deployment of submarines of the German and Italian Navies takes place calmly, without fear of active enemy actions to detect and destroy them. Consequently, submariners get the opportunity to use diesel generators (MTU 16V396SE) at any convenient time to recharge electric batteries. Accordingly, switching to fuel cells is resorted to only when there is an urgent need.
HYDROGEN INFRASTRUCTURE
The construction of coastal infrastructure facilities for the production and storage of hydrogen, as well as for refueling ships with it, has become an important part of the German program to create a submarine fleet with fuel cell VNEU. Some of the decisions taken are also relevant for Sweden, since diesel-electric submarines additionally equipped with Stirling engines are also demanding on the purity of hydrogen, as well as the potential danger of its storage.
Since the mid-70s of the last century, many European companies have joined the work in the field of hydrogen fuel, including in terms of solving issues on the topics of hydrogen storage and transportation. Automotive giants were often the pioneers here. Closer to the turn of the century, the relevant areas were actively supported and funded by EU structures. Managed from a single center, science and industry managed to find solutions to many problems, which ultimately brought a positive result. Relying on the achievements of the commercial sector, German shipbuilders have successfully coped with the creation of infrastructure for next-generation submarines.
The Type 214 export NAPS have a similar power plant to the Type 212A. It includes Siemens fuel cells and metal hydride cylinders for hydrogen storage. The operation of Type 214 submarines in Portugal and Greece has shown that they are quite suitable for relatively poor European importing countries. At the same time, German and Italian experience was widely used, which made it possible to reduce financial costs and technical risks. Having positively assessed the experience of neighboring countries, Turkey concluded an agreement with Germany on the construction of a series of ships under project 214 at a local site. The countries of the southern flank of NATO, which have purchased boats of the German project in a complete set with VNEU, rely, on the one hand, on the already created hydrogen infrastructure. On the other hand, they are expanding this infrastructure within the framework of a pan-European project, since they have joined it through the procurement and operation of the German project.
DIFFICULTIES OF THE DEVELOPING WORLD
The situation with hydrogen infrastructure in Asia and Africa is fundamentally different from what is available in Western Europe today. There is nothing to expand there – you need to create everything from scratch. If the navy wants to get the most out of underwater equipment, they need to create in their country a developed coastal infrastructure for the production and storage of hydrogen, as well as for the training of highly professional crews. Otherwise, it is impossible to achieve underwater autonomy in practice in two or three weeks.
The deployment of the necessary coastal infrastructure for this can take decades. This is too long, which encourages scientists and engineers to look for other ways to ensure the availability of hydrogen on board a submarine.
Among the solutions under consideration is the storage of hydrogen in the form of certain chemical components with their further decomposition to release hydrogen in a simple form (transformation). Currently, this path is being laid in several directions at once.
The main efforts are on the path of conversion of methanol, ethanol and diesel fuel. Other substances are also considered, including sodium borohydride, which is stored in an aqueous solution. In theory, placing these liquids on a boat and safely storing them on board is much easier to conduct compared to pure hydrogen. The volume of hydrogen contained in these liquids will be quite large. The use of the above substances has both positive and negative sides. In addition, a significant technological challenge is the development of a highly efficient conversion device suitable for placement on a submarine. In its creation, it is necessary to solve numerous issues related to the storage of fuel and other consumable liquids, mass compensation during their consumption, cooling of the power plant, etc. The issues raised have to be addressed comprehensively, since many aspects have some impact on the final technical appearance of the submarine and its characteristics, including autonomy and secrecy of actions.
conclusion
German technology is highly valued on the international market, but it has characteristic disadvantages that prevent widespread distribution around the planet. German designers are talented and inventive, but in their developments they are prone to complex technological and engineering solutions. This creates problems for operators, especially those with a lack of practical experience and the necessary skills for the competent operation of German equipment and its repair. Not everyone can boast of such high perseverance, accuracy and order, which the Germans are famous for. Perhaps today this is the biggest factor hindering the expansion of the geography of sales of German underwater equipment.
Vyacheslav Ivanov
Vyacheslav Viktorovich Ivanov is a military expert and historian.