American and British engineers have created a nozzle for laser cutters that allows them to create drones — the cutter cuts out the body, and the nozzle moves components onto it, applies contact tracks and sinters them. After that, the drone can take off directly from the cutter and get to work. The paper will be presented at the CHI 2021 conference.
As a rule, when creating prototypes of robots and drones, engineers use common components, such as Raspberry Pi microcomputers and Arduino microprocessors, as well as popular motors. Nevertheless, you still have to connect them together, check compatibility and program them yourself, so not every amateur engineer can easily create a simple robot, and even more so it is difficult for people of other professions, for example, scientists who need a drone or robot to solve an applied problem, and not by itself.
To solve this problem, there are projects that use a library of standard elements: they can be assembled into a single robot in the program, after which it issues assembly instructions and the corresponding software, and in some cases it even calculates the parameters of the engines for the kinematic model created by the user.
Engineers led by Stephanie Mueller from the Massachusetts Institute of Technology have developed a new semi-automated method for assembling drones from standard elements (the method can be applied to other devices, but the authors demonstrated it mainly on drones). Its main advantage is that the build process itself is also as automated as possible, and in fact all the user's work is reduced to interacting with the software.
As a basis, the engineers decided to take a laser cutter, which is used for cutting flat parts from large sheets or bulk, if you do not make a continuous cut in the sheet, but a recess along which two parts can be bent. The cutter is a large device with a closed body, inside of which there is a Cartesian mechanism with a suspended laser head that rides in a plane above the sheet. In addition to cutting out parts of the body to create a drone or other device, you also need to equip it with electronics and draw conductive paths between it for power and control. The authors solved this problem by creating a nozzle for the laser cutter head, which has a precursor spray for conducting tracks, and a manipulator that can drag electric motors and other components onto the cut-out parts of the body.
The nozzle has two syringes connected to a common pump. One of them works as a pneumatic gripper and can lift large components weighing up to 65 grams and small chips up to the standard size of 2010 (5 by 2.5 millimeters). The second syringe releases a paste with silver particles: it is applied to the place of the future conductive track, and then the laser of the cutter heats it and sinters it into a solid track that conducts electricity well. In the same way, the nozzle attaches the components to the body parts.
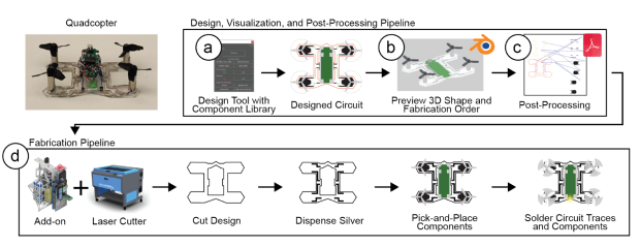
Scheme of the method
Image source: Martin Nisser et al. / CHI 2021
One of the most unusual solutions that the authors used in their work is how the nozzle receives instructions for operation. The authors decided not to use the cutter itself, since they usually have proprietary firmware installed, access to which and modification is difficult. Instead, they decided to insert additional trajectories into the plan of movements of the laser cutter head, most of which are needed to move the nozzle to the right places, and some encode the system data for the nozzle. As such a trajectory, the engineers chose a straight line with a length of three millimeters — when moving along such a trajectory, the cutter first creates a large peak acceleration on the nozzle accelerometer, and before the end of the line, a second peak acceleration with the opposite direction. This combination of accelerations is not found in normal movements during the operation of the cutter, so it can be used to give commands to the nozzle: activate or deactivate one of the two syringes.
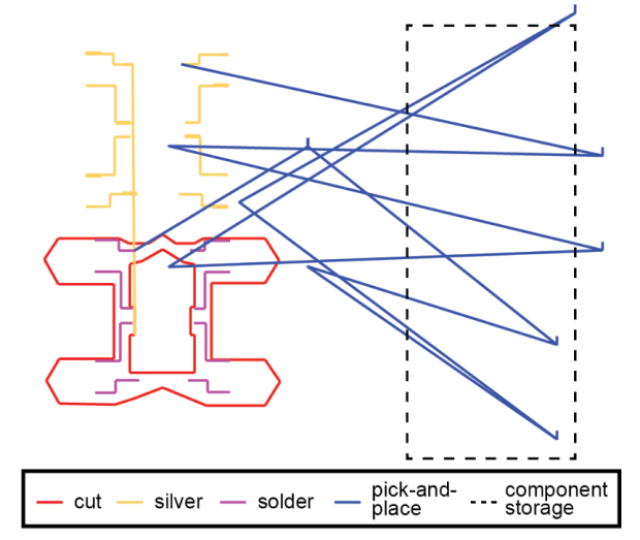
The trajectory of the laser cutter head. You can see that some of the trajectories are duplicated with an offset-the reason is that the nozzle is fixed to the side of the head. You can also notice small vertical margins on the edges of the trajectories — these are the segments that serve as commands for the nozzle
Image source: Martin Nisser et al. / CHI 2021
To create a drone or other device, the user needs to create a simple model from standard elements on a computer, place a polymer sheet for the body and parts in the cutter (they may already be there) and give the command to assemble. After that, the cutter with the nozzle itself cuts out the housing, puts the necessary components on it, for example, motors with screws and a control board, and then leads the conductive tracks to them. In the demo video, you can see that the drone is then completely ready for use and can take off directly from the cutter if its lid is open.
In 2017, another group of engineers from the Massachusetts Institute of Technology learned how to print electronic devices on a 3D printer that change their shape after printing.
Gregory Copies