Rostec United Engine Corporation introduces unique technologies for the production of blades – a key part of modern aircraft engines. The creation of a blade requires the most complex calculations in the design, the highest precision in manufacturing, as well as expensive equipment and rare metals.
Today, only six countries in the world have the competence to design and manufacture blades. Russia has once again strengthened its leadership in this industry by introducing its own latest technologies that will be used to create new aircraft engines.
From mills to aircraft engines
Each blade of a turbojet engine is the embodiment of the most advanced technologies and one of the most complex parts of the installation in production. And it all started once with the simplest devices.
The direct ancestors of modern blades in engine building can be considered the blades that drive the mechanisms of windmills and watermills. The principle of the shovel machine was used to lift liquids in the famous "Archimedean screw" and other devices of antiquity. Today, such mechanisms are used very widely − in aviation, shipbuilding, mechanical engineering, and energy.
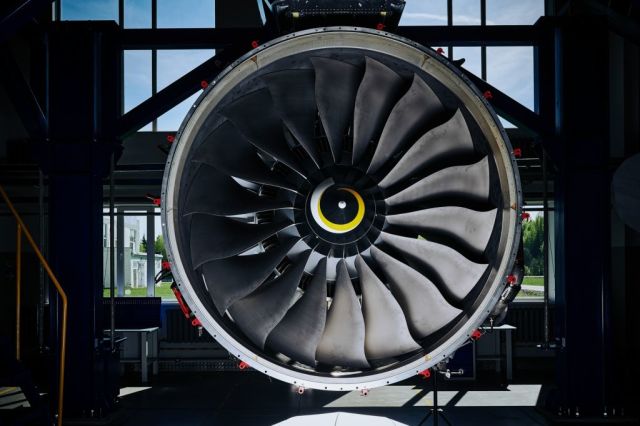
Photo: Viktor Molodtsov
It is easy to understand how the blades of a modern aircraft engine look like. The fan assembled from the blades, we see when we board the airliner. In fact, there are much more blades in the engine − their bulk is hidden under the body of the installation.
Highly loaded part
The principle of operation of a gas turbine engine, namely those that lift most modern civil and military aircraft into the sky, can be described as follows. The air enters the engine, is compressed by a compressor, heats up in the combustion chamber, rotates the turbine and is ejected from the nozzle at high speed, pushing the aircraft forward.
In the device of a gas turbine engine (GTE), several types of blades are used at once. Depending on the type of engine, these are: fan blades, low-pressure compressor blades, high-pressure compressor blades, high-pressure turbine blades, low-pressure turbine blades. In addition to these working blades, stationary blades are also used, directing the air flow.
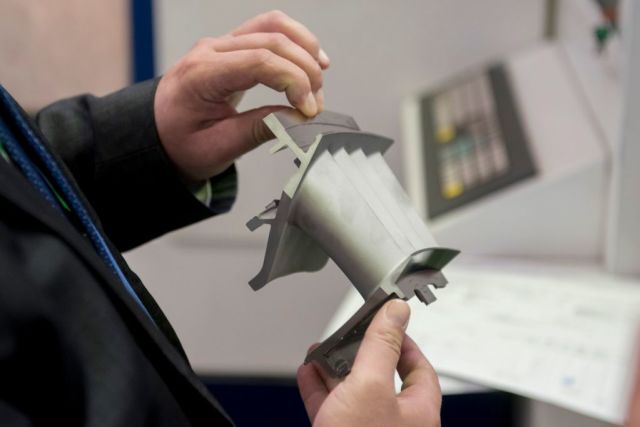
The blades of the fan and compressors work to pump and compress air, directing it into the combustion chamber. The blades in the turbine act like the blades of a windmill: the incoming air flow collides with the blades, flows around them and drives the rotor, which in turn transmits rotation to the compressor mechanism.
The cascade of high–pressure turbine blades is the most highly loaded blades in the gas turbine engine. In fact, they operate at a temperature exceeding the melting point of the metal they are made of, and the load on them is comparable to the pressure of a multi-ton truck.
The blades determine the efficiency of the main engine components (fan, compressor and turbine) and its economic parameters. About 2-3 thousand blades are used in each engine. This is the most massive part of the gas turbine engine with a complex configuration, which in turn dictates special requirements for production.
How to make "air blades"
Compressor blades are more often made by stamping with subsequent machining, and turbine blades are cast using the "single crystal" technology. A wide range of modern technologies are used in the manufacture and processing of blades: molding, casting, cutting, electrochemical processing, grinding and polishing, laser and electroerosion treatment. Technological processes of applying thermal barrier and erosion-resistant coating, vacuum heat treatment are involved. Automated measurement and control methods are used, including using lasers.
In order to influence the air flows as efficiently as possible, the blades have a complex, curved shape. In addition, special cavities are created inside the turbine blades for cooling. The blades experience a strong mechanical impact, are exposed to high temperatures and must work non-stop for many hours.
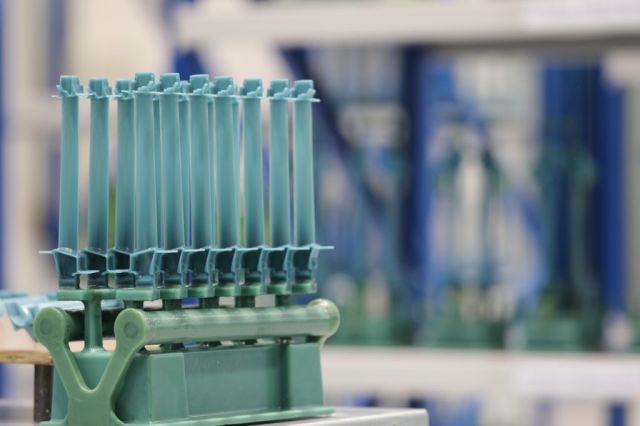
Metallurgists have been creating a material capable of withstanding such loads for a long time without losing its properties. There is almost a detective episode in the history of the creation of the first domestic jet engine. In order to get samples of the material from which the British make shovels, the Soviet delegation in 1947 went to a trick: the metal expert Sergei Kishkin managed to take out factory chips in the corrugated sole of shoes. Thus, one of the first working materials for the blades was determined to be a heat-resistant nickel alloy.
Today, metal such as titanium and polymer composite materials are used in the manufacture of fan blades. For example, for the promising PD-35 engine designed for transport and wide-body passenger aviation, the Aviadvigatel Design Bureau in Perm has developed a fan blade made of composite polymer materials. The diameter of the PD-35 fan is more than 3 meters. The transition from titanium blades to polymer blades will reduce the weight of the engine by 400 kg.
Putting competitors on the shoulder blades
In the world, only six countries have competencies in the production of turbine blades for gas turbine engines. Each company keeps its production nuances secret.
The United Engine Corporation (part of Rostec) has established centers of technological competence for the manufacture of blades. In Ufa, UEC-UMPO produces blades for combat aviation, in Rybinsk, UEC-Saturn produces blades for civil aviation, marine engines and power plants, and at UEC–Perm Motors they make high-pressure turbine blades for new promising PD-14, PD-8, PD-35.
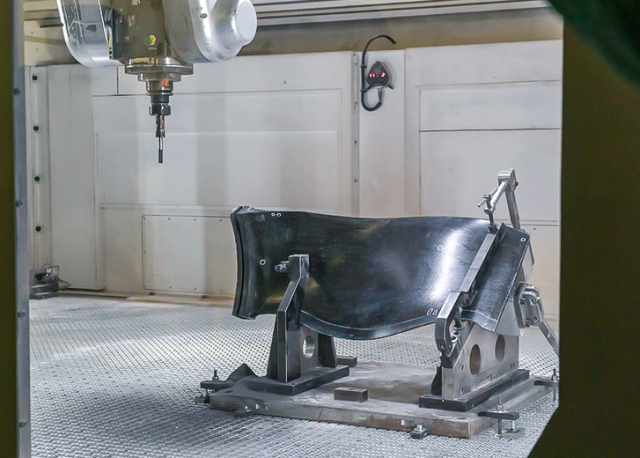
Recently, the Rybinsk enterprise introduced unique technologies for the production of compressor blades: a device for spinning high-precision titanium blades and hybrid stamping of blades made of two-phase titanium alloy. This know-how will make it possible to produce more precise parts, including large-sized ones. It is based on equipment of domestic production.
The expansion of the nomenclature of blades, different in materials, production technologies, and purpose, confirms the highest competence of Russian engine engineers. There are great achievements, and there is still a lot of work ahead to provide new Russian aircraft with new engines, the appearance of which is critically important in the conditions of sanctions.