A group of students of the Department of Metal Science and Strength Physics of NUST MISIS has started testing a new high-strength aluminum for 3D printing. It is expected that the technology developed by them will find application in aviation and mechanical engineering, as well as in other industries.
The method of SLM printing with aluminum-based composite material proposed by young researchers will allow us to abandon the use of expensive titanium, which is widely used, including in the aircraft industry.
Currently, aircraft are built using aluminum and titanium. The latter is quite expensive material. The students of nust "MISIS" Dmitry Solodov and Alexander Vasiliev suggested using a high-strength composite material based on aluminum instead of titanium. The aluminum matrix composite developed by them with the addition of refractory additives is light, which is the most important indicator in the aerospace industry, since reducing the weight of the aircraft allows you to reduce fuel consumption and, accordingly, reduce costs.
At the same time, elements from this material will be made using the so - called generative design-a technology in which artificial intelligence independently forms the appearance of parts under the parameters and restrictions set by the designer, which will further reduce the weight of aluminum products and increase the strength of structures. Then the part developed by artificial intelligence will be printed on a 3D printer using SLM printing technology, which allows you to produce complex products by laser melting of metal powder. SLM printing, as well as the use of refractory additives, will provide the material with high strength characteristics.
One of the advantages of the new technology is to reduce the cost of manufacturing complex parts with internal channels, pores, etc. At the same time, thanks to the bionic design, the mass of the finished part is significantly reduced, and the use of additive technologies and new materials will reduce the cost of finished products.
It is expected that this material will gradually replace the existing expensive titanium-based alloys, as well as those aluminum alloys that are used in the industry now. First of all, the project may be of interest to aircraft manufacturers, machine-building industries, machine-tool factories, space industry enterprises, as well as private organizations that provide 3D metal printing services.
At the moment, the first samples have already been obtained, which were tested for tension before and after heat treatment. During the tests, prototypes printed from aluminum powder with a refractory additive demonstrated higher strength compared to samples printed from conventional aluminum.
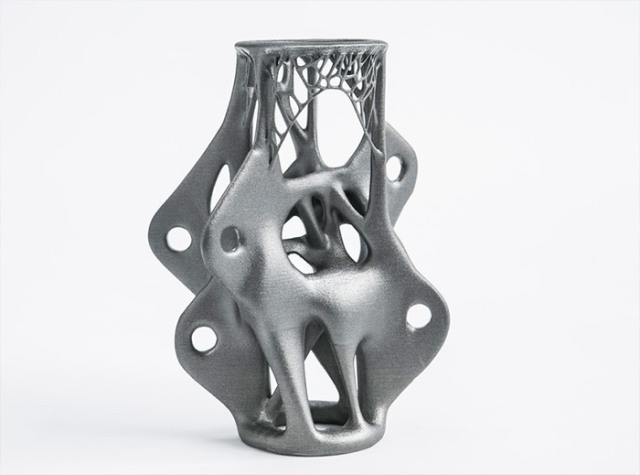