The German Rheinmetall arms concern has added a new XT class in the 4×4 variant to the autonomous ground-based robotic complexes (A–UGV, hereinafter referred to as RTK) of the Mission Master series. The diesel power plant and the one–ton load capacity are distinctive features to the previously developed 8×8 Mission Master SP (Silent Partner, Rus. - "Silent Partner").
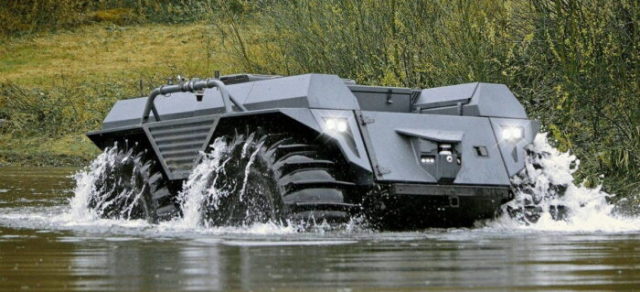
UGV Mission Master XT overcomes a water barrier
In order to expand the scope of the successful Mission Master concept, Rheinmetall changed the chassis for the new XT model, which significantly increased its payload capacity compared to the recently introduced SP variant. The size of the RTK increased to 2.57×3.72 m. As a result, with its own mass of 2.3 tons, amphibious capabilities are not limited even with the full use of a payload of one ton. The Mission Master XT diesel engine fits the car into a different logistics environment. Traditional technology primarily provides shorter maintenance periods (reduces downtime) and the use of commonly used fuels. In turn, it is recognized that the XT has lower noiselessness qualities.
The hydraulic transmission allows you to adjust the torque and braking individually for each wheel, which ensures a turn around the vertical axis. Special high-volume tires with low pressure are used for contact with the ground. The ground pressure of 0.1 bar allows the robotic complex to cross terrain unsuitable for walking. The special profile of the tires guarantees overcoming a rise of up to 70% and movement along a side slope of 40%. Tires are resistant to damage and lumbago. It is claimed that even holes with a diameter of 2.5 cm do not lead to deformation of the stable frame and does not disable the tire pressure equalization system.
To manage the RTK, an autonomous PATH kit (Proven Agnostic, Trusted Highly Autonomous) is used, developed as part of the Mission Master SP project. As standard, the operator controls his vehicle using a tablet PC, which also controls all other functionality of the installed equipment. Sensors provide information about the environment around the vehicle, which, among other things, is evaluated using artificial intelligence and displayed to the operator on maps. The proposed "picture" includes the recognition of the path and obstacles, the display of the goal, its classification and tracking. Route and mission planning is supported. The operator can choose between "follow me" mode (in which the vehicle follows a person or other vehicle walking ahead at a fixed distance) or autonomous mode (in which the Mission Master finds the way to the destination using only control points on the route).
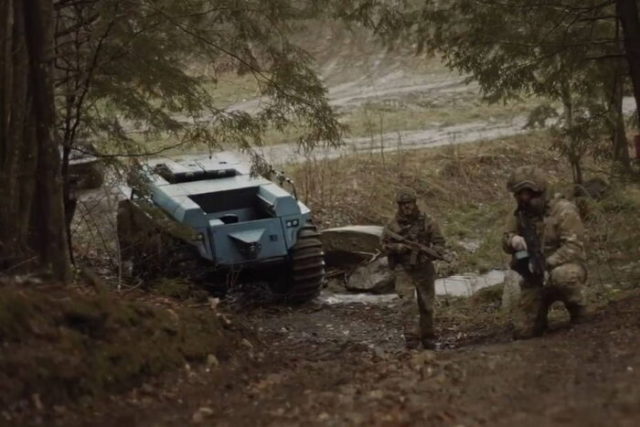
Mission Master XT follows the Head Watch
To facilitate the operator's work and optimize actions on the route, the tire pressure monitoring system is able to adjust it automatically, in accordance with the nature of the soil, thus ensuring constant and optimal traction.
The robotic complex of the XT model can also be controlled "from a machine". The vehicle's own controls were retained. The driver can sit down and directly drive the car, for example, in a field camp or during repairs.
With a maximum weight of 3.3 tons, the XT can be transported on the external suspension of helicopters (CH-53 or CH-47) or in the cargo compartment of transport aircraft such as C-130 and more. UGV is suitable for parachuting. The dimensions of the unmanned vehicle also allow the use of ISO standard containers for land and sea transport.
The presented Mission Master XT is a cargo version and, in a sense, a basic configuration. This means that the entire payload mass (1 ton) can be used for transportation. The modular chassis is designed to accommodate the mission payload. To this end, Rheinmetall is preparing a number of sets of equipment, including equipment for combat support (with machine guns, automatic guns of various calibers, launchers for missiles and UAVs, as well as modules for reconnaissance and/or drone warfare). Individual modules are developed according to the needs of the customer.
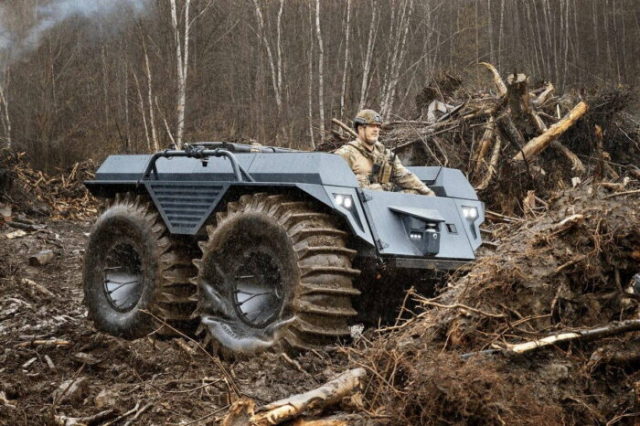
Mission Master XT management "from the machine"
The application functionality is managed using the tablet PC mentioned above. You can also use other mobile devices: smartphones or smart watches. The use of weapons always requires continuous monitoring by the operator.
It is reported that it takes no more than 14 months for the manufacturer to convert the base model into a Mission Master with applied functionality. The rather short period is explained by the experience gained by Rheinmetall on the SP project. After the completion of internal testing, the XT will be ready for mass production in the next few weeks, and then will go on tour to potential customers.
TTX Mission Master in Comparison
Mission Master XT Mission Master SP Length/width, m 2,57/3,72 2,95/1,55 Empty weight, kg 2 217 750 Load capacity, kg 1 000 600 Drive Diesel, 50kW Electric motor Speed (max), km/h 40 30 Speed on the water (max), km/h 5 5 (with reduced load) Range of travel, km 750 900 Operating time in silent mode, hours 6 72 Air mobility External: CH-53 / CH-47 internal: from C-130 and more Internal CH-53 / CH-47 Equipment Desantirov. with a parachute; Control is pressed. in tires; Required. antifriction. features Desantirov. with a parachute; Tires without pressure; tracks as an option.
According to representatives of the concern, the next step in the development of the project is already on the agenda. At the request of the customer, the hybrid drive version and the main functions of the SP and XT can be implemented on the same platform.
According to the materials of the resource soldat-und-technik.de