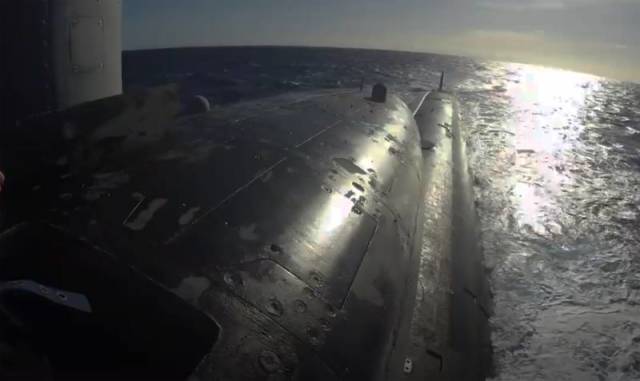
Image source: topwar.ru
Using parts created by a 3D printer reduces costs and reduces the production time of ships worth billions of dollars, which are created over the years.
Huntington Ingalls Industries has announced that its Newport News shipbuilding division has received permission to use printed pipe fittings or other potential components in the construction of aircraft carriers and submarines.
Dave Bolkar, vice president of engineering and design at Newport News, said.
Three Gerald R. Ford-class aircraft carriers and Columbia and Virginia-class submarines are being built at the Newport News shipyard. The dates of final readiness are scattered throughout the next decade.
USS George Washington (CVN-73) and USS John C. Stennis (CVN-74) are undergoing refueling and overhaul. Washington began refueling and comprehensive repairs at the Newport News shipyard in August 2017, and Stennis arrived in May 2021.
According to Huntington Ingalls representative Todd Corillo, it is not known exactly how much time and money can be saved on construction and major repairs thanks to 3D-printed stainless steel parts.
Todd Corillo said.
Newport News Shipbuilding has been working on the introduction of 3D printing, also known as additive technology, at shipyards for more than 15 years. This method was first approved in October 2018, when the Naval Marine Systems Command announced that a prototype of a metal drainage filter printed on a 3D printer would be installed on the aircraft carrier Harry S. Truman (CVN 75) built in Newport News.
Eventually, in 2019, a pipeline assembly printed on a 3D printer was installed on the ship for the first time. The shipyard in Newport News is seeking additional permits for the manufacture of 3D printers for wider use and the introduction of printed parts.