Developed by the Israeli private company Robotican, the Rooster hybrid UAV ("Rooster") is designed to conduct reconnaissance in confined spaces, such as buildings and underground structures. After October 7, 2023, the product is actively used by the Israel Defense Forces (IDF) and Israeli rescue teams. It was adopted by the special operations forces of the United States and Europe, as a result of which the system was assigned a NATO inventory number.
Robotican company, founded in 2013 by a small group of Israeli engineers and scientists. The total number of employees is about 50, of which 37 are engineers and graduates of computer science faculties. The company is actively engaged in the development of autonomous robotic systems.
Like all Robotican products, the Rooster hybrid UAV was created based on an original idea that originated within the company. All subsequent stages – development, production, quality control, delivery, and customer support – are also performed in-house. According to a Robotican representative: "At the concept development stage, we wanted to create something that could eliminate the disadvantages of other drones when used indoors or underground."
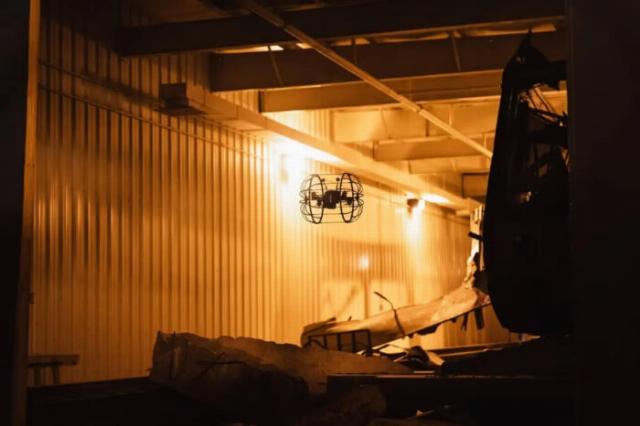
Indoor Rooster Hybrid UAV
The Rooster is an unmanned aerial vehicle with a central body housing electronics, batteries, antennas and an optoelectronic sensor with a Full-HD Low-Level television camera operating in the near infrared range. The camera's field of view is 130° horizontally and 90° vertically, which provides good situational awareness both during flight and during static observation.
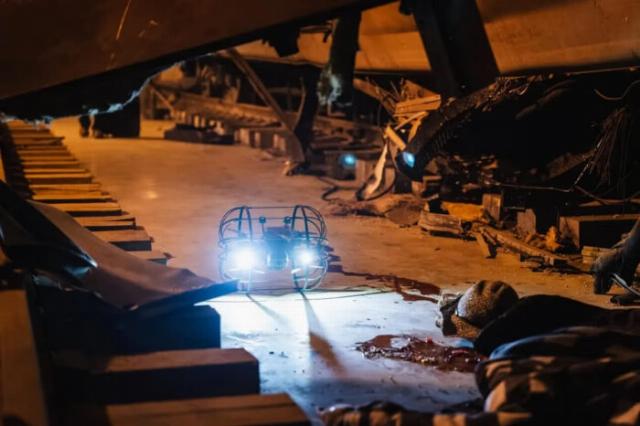
Rooster: operation of light sources
The system is equipped with two 2200 lumens visible light sources and two infrared light sources. Four manipulators are equipped with electric motors that drive three-bladed screws. On the front manipulators, the screws are located under them, and on the rear ones, above them. Hemispherical frames are located on both sides of the UAV, which are connected by beams. The whole structure is very light, but at the same time durable. It protects the rotors during flight if the Rooster crashes into a wall while moving in a confined space (According to Robotican, when launching a UAV inside a building with exposed propellers, only one out of five drones "survives").
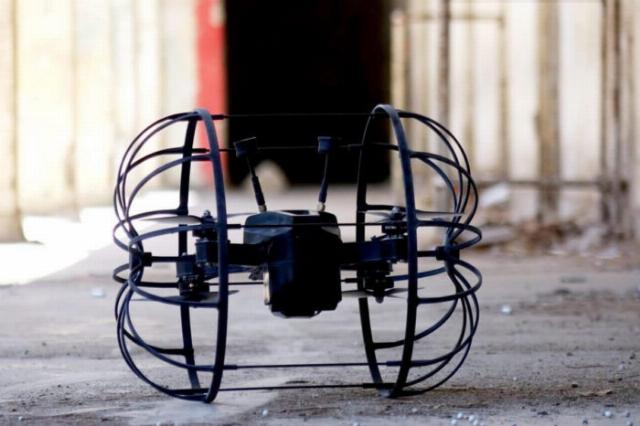
Movement on frame wheels in the building
The second function of wireframes is equally important. Since the cage frames are not rigidly fixed to the body of the UAV, they turn into "wheels". By using the thrust of the rotors at a low number of revolutions per minute, they allow the Rooster to roll along the surface of the earth, similar to a ground vehicle. The "wheels" have a diameter of 316 mm, and the total width of the frames is 400 mm.
The hybrid solution for moving through the air and on the ground has played a key role in solving the problem of autonomy, as batteries are still one of the most important elements in electrically powered systems. The flight time of one Rooster is 12 minutes, and the driving time on wheels is 30 minutes. As a rule, the Robotican hybrid UAV flies when encountering stairs or other obstacles and moves on wheels when possible and high speed is not required, so the actual autonomy of movement is somewhere between these two indicators.
Three operating modes are available: ground control mode, when the robot moves on the ground; height control mode, in which the height above the surface is adjusted automatically; and positioning mode, in which height is adjusted and obstacles are avoided. However, Rooster is not always on the move: it can stay in place and observe what is happening, tracking any possible movement or other events. In this case, the battery life increases, because when the Rooster is stationary, the power consumption is limited by communication and sensor operation, which allows you to increase the battery life to 4 hours.
The Rooster weighs about 1,650 grams, including an integrated optoelectronic system and a battery. In the upper part of the "fuselage" there is a mounting bracket for mounting an additional payload weighing up to 300 grams. The payload mass can be increased to 500 grams, but this will greatly reduce the duration of the flight.
At the moment, the manufacturer has developed four payload options: the OS-91 oxygen sensor, the RS-X5 radiation sensor, the TC-54 thermal imaging camera and an untitled warhead. Some of them are more suitable for rescue operations, while others are designed for military tactical operations, especially the warhead developed by order of special forces units. Special sensors are purchased on the market, and then their optimal integration with Rooster is ensured. In the case of the warhead, Robotican engineers have developed a remote-controlled ignition system from a portable control panel (MCU), as well as safety procedures. The high explosive or shaped charge is provided by third parties. In this case, the Rooster turns into a kamikaze drone.
A unique feature of the Rooster system is the ability to organize self-repairing network communication, which increases the efficiency of using the drone during operations underground. A reliable DTC (Direct to Cell) communication line is used, operating in the 2.1–2.5 GHz band, which, upon customer request, can provide 128-bit encryption.
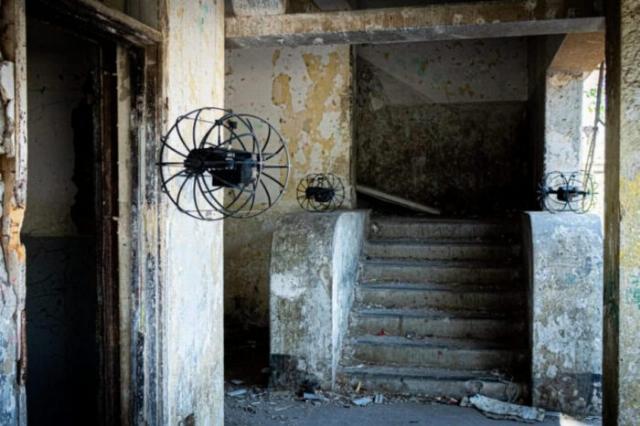
Rooster hybrid UAVs in the group
Building a network connection. During a normal operation in a tunnel, the first drone conducts reconnaissance and finds the entrance to the tunnel, after which it penetrates it. When the control system warns the operator about a low signal level, the Rooster lands in the most convenient place for observation. The second robot is immediately launched, which quickly overcomes the distance to the first robot and penetrates deeper into the tunnel. Robot No. 1 acts as a radio repeater. When the motion control system gives the next signal, the second robot lands. A third one is launched, which moves even further, so that in the end the operator gets three different types of tunnel that allow him to control the situation. Rooster has artificial intelligence-based algorithms that automatically detect images and objects. Depending on the data sets provided by the customer, the system is able to learn not only to detect, but also to recognize images and objects (for example, weapons, booby traps, faces).
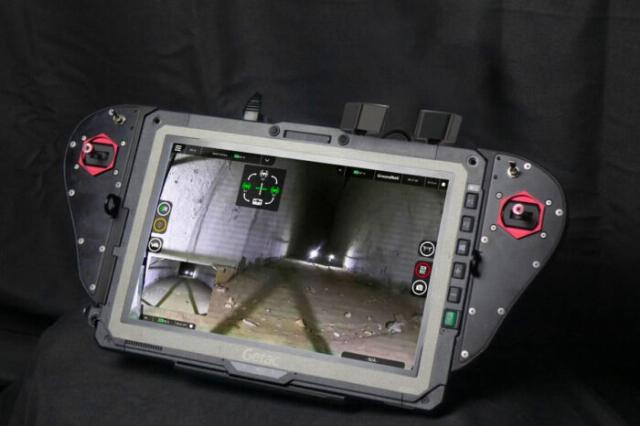
Portable control panel
All this significantly reduces the burden on the operator while accelerating the pace of mission performance. The current configuration of Rooster allows you to connect up to three robots, the limitation is related to the available bandwidth of the control panel, all broadcast images are displayed as an icon at the bottom of its display. The operator clicks on the icon of the robot he wants to control.
Robotican offers a set of three hybrid Rooster UAVs and one control panel. They are packed in a sturdy case measuring 814×387.7×586.5 mm. A tactical backpack is also available: its base measures 42x35 cm, height is 53 cm, and the total weight when loaded with the Rooster kit is 8.4 kg. The backpack is equipped with foam inserts to protect it from damage during transportation. The two drones are in the bottom of the backpack in disassembled form and can be ready for operation in one minute. There is one fully assembled and ready-to-launch Rooster and a control panel on top.
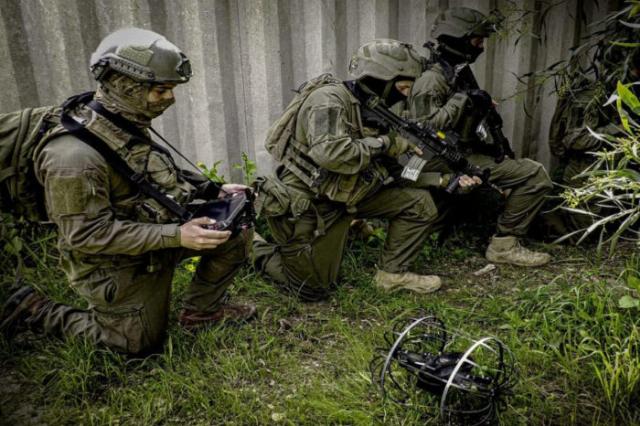
The work of the Rooster UAV operator
Other accessories allow the commander to view the same video recording that the operator receives in real time and, if necessary, direct him during the task. The video stream can also be redirected to a higher-level command post using the LiveU streamer built into the flight control system, which can use both cellular and satellite communications.
For educational purposes, the system can be supplemented with full-fledged learning software developed by Robotican. Robotican has officially announced the sale of several dozen Rooster kits to European special forces, rapid reaction units and infantry units, which allowed them to receive a NATO license plate.
Source: edrmagazine.eu