Nust MISIS scientists have improved the technology of 3D printing from aluminum, achieving an increase in the hardness of products by one and a half times. The developed nanocarbon additive to aluminum powder obtained from products of associated petroleum gas processing will improve the quality of aerospace composites printed on a 3D printer.
Today, the main application of 3D printing from aluminum is the creation of high-tech parts for the aviation and space industries. The presence of even the smallest defects in printed structures is critical for the safety of the created equipment. According to nust MISIS scientists, the main risk of such defects is the high porosity of the material caused, among other things, by the quality of the original aluminum powder.
To ensure a uniform and dense microstructure of printed products, MISIS Catalis Lab scientists proposed adding carbon nanofibers to aluminum powder. The use of this modifying additive makes it possible to ensure low porosity of the material and increase its hardness by one and a half times.
The technology of synthesis of nanocarbon additives developed by the research team includes methods of chemical deposition, ultrasonic treatment and IR heat treatment.
The study was conducted jointly with specialists Of the Institute of catalysis SB RAS. In the future, the research team plans to determine the optimal conditions for selective laser melting of new composite powders, as well as to develop a technology for post-processing and industrial use of synthesized products.
The results of the study are published in the international scientific journal Composites Communications .
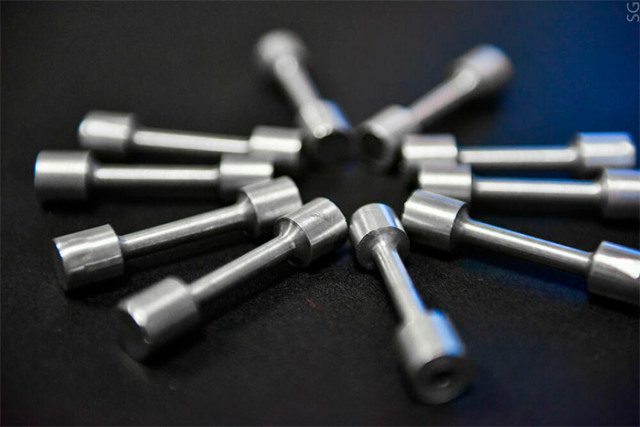
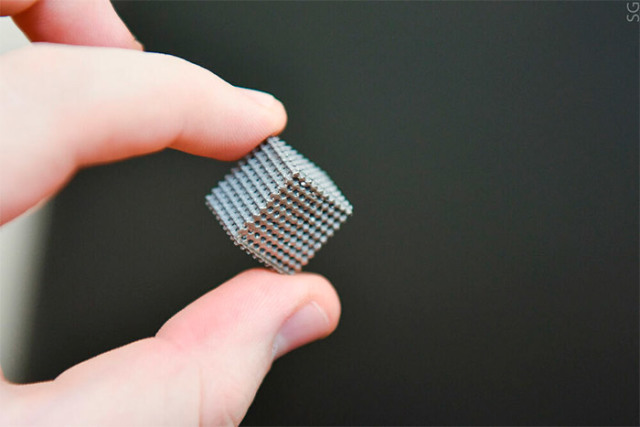
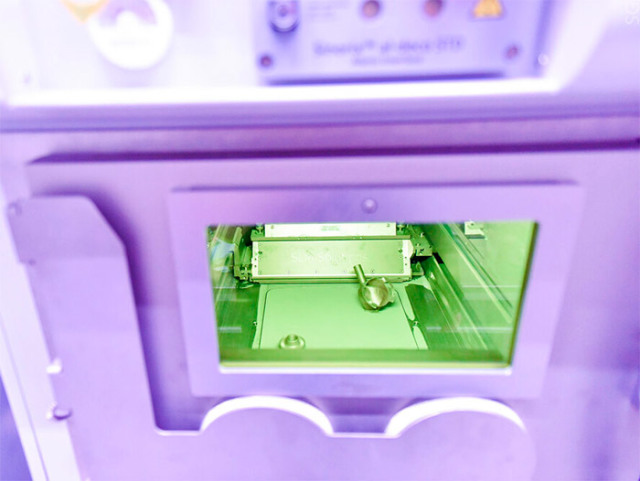
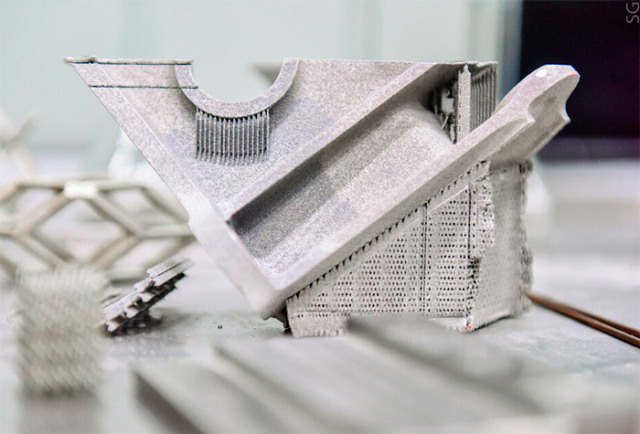