Как добиться оптимального соотношения характеристики вооружения/цена?
29 сообщений, отображено с 21 по 33
№17
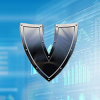
Андрей Л.
03.10.2012 11:05
Цитата
TWI (обучение на производстве), один из наименее затратных и весьма результативный способ кардинального изменения ситуации к лучшему. Эти методы без дополнительных инвестиций в оборудование могут давать эффект увеличения выработки на 60% за 9 месяцев и выше.
Не может! Только подготовка персонала методам улучшения ничего не дает. Я знаю предприятие на котором стимулируется подача заявок на улучшение - даже если улучшение будет незначительным человек всё равно получает бонусы за инициативу. По факту предприятие постоянно несет серьезные доп. затраты на содержание персонала по анализу и проверке заявок. а также на модернизацию - потому что, как правило, сами инициативы от рабочих носят характер улучшения с модернизацией их рабочего места или смежных мест, с которыми от контактирует по цепочке.
Философия предприятия, по умышленному увеличению расходов по данной тематике, звучит так - из тысяч предложений выстрелит одно или два, которые смогут окупить все затраты. Но это - философия, которая никак не может вязаться со статистикой, тем более в 60% ...
Цитата
в которой основное внимание уделяется устранению брака за счет применения таких приемов, когда ставка делается на анализ результатов измерений и совершенствование процессов.
Это философское понятие к сожалению не определяет методов и направлений контроля, оно лишь
1. предлагает механизм расчета
2. определяет необходимость изначальных затрат на сбор статистики, её ведение и углубленный анализ для локализации мест возникновения отклонений.
А лекарство надо будет всё равно искать и придумывать самим.
При этом, чем сложнее техпроцесс и чем больше размером цех, тем большие затраты на измерения и места контроля необходимо будет нести. И это ещё до видимого результата. Теория очень интересна, но для современного не серийного производства (а у нас на предприятиях ВПК давно уже нет серий как при СССР, и в Роскосмоссе в виду специфики в первую очередь) в сфере ВПК - этот метод вряд ли будет эффективен.
Для того, чтобы привести задачу в текущим условиям в ВПК, давайте добавим условие - начальные затраты на определение мест возникновения брака и выявления причин должны быть минимальны.
0
Сообщить
№18

Сергей Смирнов
03.10.2012 11:55
Цитата, Андрей от 03.10.2012 11:05 »
Не может! Только подготовка персонала методам улучшения ничего не дает.
Хорошей иллюстрацией для осознания того, что это может быть, а самое главное есть и в нашей стране, иллюстрирует статья «Я в рабочие пойду, пусть меня научат!» http://kr-znamya.ru/index.php?option=com_content&view=article&id=5302:2012-06-01-10-29-23&catid=35:econom&Itemid=67, характеризующая такой подход к работе.
0
Сообщить
№19

Сергей Смирнов
03.10.2012 14:13
Цитата, Андрей от 03.10.2012 11:05 »
А лекарство надо будет всё равно искать и придумывать самим.
При этом, чем сложнее техпроцесс и чем больше размером цех, тем большие затраты на измерения и места контроля необходимо будет нести.
Любим мы все усложнять. Любое рабочее место, участок, цех, это совокупность трех элементов ВСЕГО ТРЕХ!!!
1. Человек
2. Средство производства
3. Предмет труда
Взаимодействие этих элементов во времени организовывают производственный процесс или процесс добавления ценности. И ВСЕ!!!
Будь то ларек или космический корабль.
И научившись определять эффективность использования рабочего времени по этим трем элементам мы получаем с Вами универсальный инструмент улучшения и повышения производительности любой производственной системы.
0
Сообщить
№20

Сергей Смирнов
03.10.2012 14:17
Цитата, Андрей от 03.10.2012 11:05 »
Теория очень интересна, но для современного не серийного производства (а у нас на предприятиях ВПК давно уже нет серий как при СССР, и в Роскосмоссе в виду специфики в первую очередь) в сфере ВПК - этот метод вряд ли будет эффективен.
Опять про усложнение: Даже при единичном производстве, рабочему на токарном станке все равно какую деталь точить, другое дело если он 40 минут ищет инструмент, или заготовки не подвезли, или оборудование как всегда внепланово сломалось или того хуже не обеспечивает необходимый класс точности, или тех документация не актуализирована... продолжать можно бесконечно. Вы не хуже меня знаете реалии постсоветского производства
0
Сообщить
№21

Сергей Смирнов
03.10.2012 14:23
Цитата, Андрей от 03.10.2012 11:05 »
Для того, чтобы привести задачу в текущим условиям в ВПК, давайте добавим условие - начальные затраты на определение мест возникновения брака и выявления причин должны быть минимальны.
Научите рабочих вести контрольные карты Шухарта. Но для начала нужно научить этому Всю вертикаль власти, а еще лучше скорректировать парадигму управления. :-)
Как летают деньги в космической отрасли
Российские космические технологии сейчас обходятся дорого и вскоре могут оказаться ненужными
http://www.vedomosti.ru/library/news/4481671/biznes_na_orbite
0
Сообщить
№22
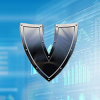
Андрей Л.
03.10.2012 15:49
В статье "Я в рабочие пойду, пусть меня научат!" много демагогии о бережливом производстве, но обе рацухи, которые были приведены сводятся к тому о чем я говорил выше - сделайте затраты на производство и получите эффект. Причем не факт, что эффект будет большим.
Первый случай, когда каждый рабочий сам у станка шаманил, но не было технолога - это простите просто вандализм, особенно если учесть, что все новые станки идут с сетевыми картами и надо наверное было догадаться зачем они нужны.
Тем не менее, если не было технолога и централизованного доступа к картам раскроя это значит, что задачи компьютеризации каждого рабочего места и централизация места хранения карт решались вместе. Это огромные затраты, которые на производстве несут в себе не только стоимость оборудования как клиентских мест, так и серверов, но и защиту клиентских рабочих мест и сетевой инфраструктуры от повреждений.
Кстати сама по себе задача раскроя очень сложная и каждый решает её по разному. Только на оптимизации и унификации сортамента под раскрой и модели кроя можно было сэкономить огромные деньги - не затратив практически ничего.
Ни в чем статья не убедила.
Я был на нескольких семинарах с участием предприятий ВПК, на которых пытались рассказывать об успехах применения Lean в России. Рассказы были красивы до поры выхода начальников цехов и производств на трибуну или до их ответов с места.
Я УВЕРЕН В ТОМ ЧТО LEAN В РОССИИ ПРИЖИВЕТСЯ - для этой технологии в России слишком благодатная почва, чтобы произошло отторжение, но будет это не раньше, чем предприятия научаться понимать, что им надо оптимизировать. А пока - такого понимания, в большинстве случаев, просто нет.
Заводы научились считать деньги и тратить их просто так, на "попробовать ещё вот такую технологию" ни у кого особого желания нет.
Цифры, которые называются по успехам применения технологий
1. не доказуемы
2. могут содержать в себе не чистый эффект именно от этих мероприятий.
По усложнению.
Вы в принципе не согласны с тем, что чем сложнее система, тем сложнее и затратнее становится её организация и совершенствование, пусть даже без наращивания числа сущностный оптимизации: Человек, Средство производства, Предмет труда?
Мы снова ушли в демагогию. Давайте по конкретным шагам. Структуры я назвал. Жду предложений не технологий, котоыре можно было бы попробовать, а конкретно, что можно сделать исходя из Вашего опыта.
Первый случай, когда каждый рабочий сам у станка шаманил, но не было технолога - это простите просто вандализм, особенно если учесть, что все новые станки идут с сетевыми картами и надо наверное было догадаться зачем они нужны.
Тем не менее, если не было технолога и централизованного доступа к картам раскроя это значит, что задачи компьютеризации каждого рабочего места и централизация места хранения карт решались вместе. Это огромные затраты, которые на производстве несут в себе не только стоимость оборудования как клиентских мест, так и серверов, но и защиту клиентских рабочих мест и сетевой инфраструктуры от повреждений.
Кстати сама по себе задача раскроя очень сложная и каждый решает её по разному. Только на оптимизации и унификации сортамента под раскрой и модели кроя можно было сэкономить огромные деньги - не затратив практически ничего.
Ни в чем статья не убедила.
Я был на нескольких семинарах с участием предприятий ВПК, на которых пытались рассказывать об успехах применения Lean в России. Рассказы были красивы до поры выхода начальников цехов и производств на трибуну или до их ответов с места.
Я УВЕРЕН В ТОМ ЧТО LEAN В РОССИИ ПРИЖИВЕТСЯ - для этой технологии в России слишком благодатная почва, чтобы произошло отторжение, но будет это не раньше, чем предприятия научаться понимать, что им надо оптимизировать. А пока - такого понимания, в большинстве случаев, просто нет.
Заводы научились считать деньги и тратить их просто так, на "попробовать ещё вот такую технологию" ни у кого особого желания нет.
Цифры, которые называются по успехам применения технологий
1. не доказуемы
2. могут содержать в себе не чистый эффект именно от этих мероприятий.
По усложнению.
Вы в принципе не согласны с тем, что чем сложнее система, тем сложнее и затратнее становится её организация и совершенствование, пусть даже без наращивания числа сущностный оптимизации: Человек, Средство производства, Предмет труда?
Мы снова ушли в демагогию. Давайте по конкретным шагам. Структуры я назвал. Жду предложений не технологий, котоыре можно было бы попробовать, а конкретно, что можно сделать исходя из Вашего опыта.
0
Сообщить
№23
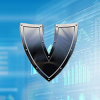
Андрей Л.
03.10.2012 15:54
Цитата
Но для начала нужно научить этому Всю вертикаль власти, а еще лучше скорректировать парадигму управления. :-)
Это общие слова, за которыми стоят крупные суммы на обучение без гарантированного результата. Мы представляем, что такое обучить всю вертикаль управления со сложившимся менталитетом и на предприятии, о котором преподаватели или консалтинговая компания имеют очень и очень поверхностное понимание. Даже если будет проведено экспресс или полноценное обследование - всё равно я не видел, даже за большие деньги, качественного обследования, после которого не то, что пол компании консалтеров будут понимать хорошо компанию, которую обследовали, но даже специалисты, занимающиеся обследованием имеют о ней весьма примитивное понимание.
Ну а уж о парадигме я вообще не буду лучше говорить. Это не тот случай когда БАЦ и... новая парадигма :)
0
Сообщить
№24

Сергей Смирнов
03.10.2012 16:07
Цитата, Андрей от 03.10.2012 15:49 »
В статье "Я в рабочие пойду, пусть меня научат!" много демагогии о бережливом производстве, но обе рацухи, которые были приведены сводятся к тому о чем я говорил выше - сделайте затраты на производство и получите эффект
К сожалению Вы не уловили главного в этой статье: Атмосферы сотрудничества и вовлеченности персонала в процесс повышения производительности труда которые и позволяют получать впечатляющие результаты.
"Главная цель обучения - развить потенциал рабочих, готовых стать своеобразными «моторами» на производстве, умеющими распространять свои идеи и знания.
- Все годы моей работы на мебельной фабрике мы отбирали и воспитывали рабочих, чтобы получить специалистов нового типа, таких же, какие есть на «Металлисте», - говорит Карим Касимов. – Сейчас на производстве трудятся 300 основных рабочих. Но чтобы все они хорошо и эффективно работали, нужно в идеале 70 «моторов», которые будут вести за собой. Подавать рацпредложения, не только технические, но и организационные, экономические. И задача руководства – создать такую атмосферу на предприятии, чтобы был фонтан идей, предложений по борьбе с нежелательными явлениями. Выявив их, тут же устранять. Очень важно, чтобы ни одна инициатива не осталась незамеченной. Работник должен видеть, как его идеи, пусть даже небольшие, ценятся предприятием, как их реализуют. Иначе фонтан заилит, превратится в болото, и все останется как прежде. Так что пришла пора вновь обучать «верхи». Останавливать этот процесс не собираемся."
Кстати, за три года фабрика увеличила выпуск продукции в 2 раза и в годы кризиса 2008 года единственная в России увеличившая выпуск и продажи продукции. Как Вы думаете за счет чего?
0
Сообщить
№25

Сергей Смирнов
03.10.2012 16:18
Цитата, Сергей от 03.10.2012 14:23 »
Я УВЕРЕН В ТОМ ЧТО LEAN В РОССИИ ПРИЖИВЕТСЯ - для этой технологии в России слишком благодатная почва, чтобы произошло отторжение, но будет это не раньше, чем предприятия научаться понимать, что им надо оптимизировать. А пока - такого понимания, в большинстве случаев, просто нет.
Согласен с Вами, что понимания просто нет. И это еще одна проблема СИСТЕМНАЯ, проблема профессионального образования. Но это отдельная тема...
Я не являюсь приверженцем LEAN, но использую все методы в своей работе направленные на Повышение производительности предприятия как системы и LEAN, и НОТ, и ТОС, и управление групповой динамикой, и психологические аспекты управления изменениями.
Цитата, Сергей от 03.10.2012 14:23 »
Заводы научились считать деньги и тратить их просто так, на "попробовать ещё вот такую технологию" ни у кого особого желания нет.
И это еще раз подтверждает мысль что улучшение ради улучшения бессмыслено. Рассел Акофф высказал замечательную мысль: "Мы все научились решать проблемы, но очень часто решаем не ту" :-)
0
Сообщить
№26

Сергей Смирнов
03.10.2012 16:31
Цитата, Андрей от 03.10.2012 15:49 »
По усложнению.
Вы в принципе не согласны с тем, что чем сложнее система, тем сложнее и затратнее становится её организация и совершенствование, пусть даже без наращивания числа сущностный оптимизации: Человек, Средство производства, Предмет труда?
Почему не согласен? Согласен полностью с Вами. Содержать ларек существенно менее затратно чем к примеру:
"В качестве примера, Рогозин привел предприятие "Ижмаш", которое занимает избыточную площадь. "Мало кто знает, но при проектировании и строительстве этого завода-гиганта закладывалась возможность выпускать совсем другую продукцию, а вовсе не автоматы и пулеметы", - пояснил вице-премьер. При этом он отметил, размеры "Ижмаша" позволяют "строить авианосцы", хотя "там производят только автоматы Калашникова" http://vpk.name/news/76001_rogozin_predlozhil_napomnit_oboronke_o_1930h_godah.html
0
Сообщить
№27

Сергей Смирнов
03.10.2012 16:43
Цитата, Андрей от 03.10.2012 15:49 »
Структуры я назвал. Жду предложений не технологий, котоыре можно было бы попробовать, а конкретно, что можно сделать исходя из Вашего опыта.
я так понимаю :-)
Цитата, Андрей от 03.10.2012 11:05 »
Для того, чтобы привести задачу в текущим условиям в ВПК, давайте добавим условие - начальные затраты на определение мест возникновения брака и выявления причин должны быть минимальны.
Я и написал, обучаем рабочих на станках, работе с картами Шухарта, в которые вносим отклонения при обработке деталей, и на ранней стадии начинаем отслеживать стабильность процессов, задолго определяя что процесс теряет стабильность, а не тогда когда "запороли" партию в 1000 деталей. Действенный рабочий а главное результативный инструмент.
Затраты на обучение минимальны, а эффект зависит от того количества брака с вытекающими из этого затратами которые вы имеете на производстве.
0
Сообщить
№28
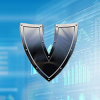
Андрей Л.
04.10.2012 14:19
Честно признаюсь не знаю зачем нам расчеты квадратичных отклонений, когда есть четкое отклонение от норм и можно установить критерий объемов брака от статистики и задать объемы снижение во времени, с которыми и сравнивать.
Но мне то хотелось бы, чтобы мы с Вами, и если ещё кто-то к беседе подключиться с ними, составили перечень критериев по которым можно вести такое сравнение, которые можно задать и проверить без преобразований (ну или если есть прямо нестерпимое желание перейти к доп. расчетам - то и посчитать со сбором статистики по большому числу к периодов или сокращая размер периода до контрольных точек).
Но мне то хотелось бы, чтобы мы с Вами, и если ещё кто-то к беседе подключиться с ними, составили перечень критериев по которым можно вести такое сравнение, которые можно задать и проверить без преобразований (ну или если есть прямо нестерпимое желание перейти к доп. расчетам - то и посчитать со сбором статистики по большому числу к периодов или сокращая размер периода до контрольных точек).
0
Сообщить