ММЗ «Авангард» исполнилось 80 лет
Московский машиностроительный завод «Авангард» – предприятие, закрытое до крайности, поскольку его продукция хоть и широко известна в мире, но секретна. Только здесь производят управляемые ракеты для зенитных комплексов С-300 и С-400. Так что немногие могут попасть на территорию. Корреспонденту «ВПК» в канун юбилея удалось увидеть, как создается легендарное оружие для комплексов ПВО. Впрочем, весьма плотно на «Авангарде» занимаются поиском своей ниши и на ниве производства гражданской продукции.
Как куется ракетный щит России
В пятидесятых годах прошлого столетия на ММЗ «Авангард» выпускали ракеты для противовоздушной обороны С-25, С-75. В заводском музее хранится обломок самолета-шпиона U-2 американского пилота Гэри Пауэрса, сбитого 1 мая 1960 года вблизи Свердловска. В составе 11 зенитных ракетных полков вьетнамской народной армии советские комплексы «Двина» охраняли небо и добивались весьма эффектных побед. Практически во всех ближневосточных военных конфликтах несли боевую службу батареи советских комплексов ПВО, оснащенных ракетами, сделанными в цехах этого московского предприятия. Затем пришло время для производства лучших в мире ЗУР для комплексов С-300 и С-400.
Завод «Авангард» уникален тем, что в его цехах собран весь производственный цикл – от создания заготовок до сборки ракеты. Только снаряжение БЧ происходит в другом месте.
“Завод «Авангард» уникален тем, что в его цехах собран весь производственный цикл – от создания заготовок до сборки ракеты. Только снаряжение БЧ происходит в другом месте”
Стартует производство зенитных ракет в кузнечно-прессовом горячем цехе. Здесь в прямом смысле этого слова куют ракетный щит Родины. Раскаленная заготовка ложится на стол трехтонного паровоздушного штамповочного молота, и после серии ударов заготовка газового руля ракеты готова.
По словам начальника цеха Тафкила Аюпова, в его хозяйстве могут отковать деталь из любого металла – углеродистых и легированных сталей, титанового сплава. Наряду со сталями здесь обрабатывают и алюминиевые сплавы. Из них делают защитные колпаки транспортно-пусковых контейнеров.
Следующий этап рождения ракеты проходит в механосборочном цехе. Там царство современных станков с ЧПУ. При этом, по словам заместителя главного технолога Александра Ушакова, нет оборудования, покупка которого находится под западными санкциями. Станки по большей части отечественные и именно на них изготавливают аэродинамические элементы крыльев.
На многих предприятиях российского оборонпрома одной из главных проблем была да и, что греха таить, остается проблема простоев станочного парка. Была она и на этом участке. По словам Ушакова, на «Авангарде» ее решили. Здесь работает система отслеживания времени работы станков.
У каждого станка стоят терминалы, на которых автоматически фиксируется состояние оборудования.
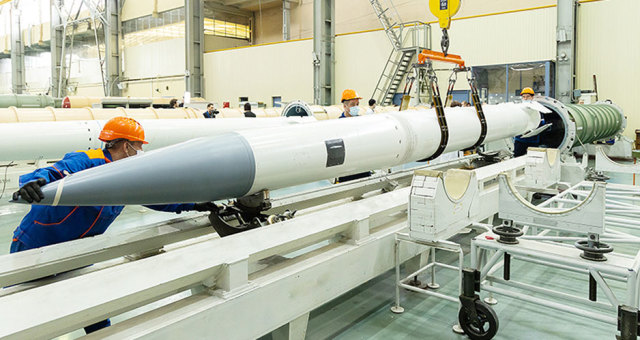
...Ракета на старте
«Но оператор обрабатывающего центра может ввести информацию и вручную, – говорит начальник бюро инструментального хозяйства Андрей Непогожев. – Наблюдение идет в режиме реального времени и в любой момент можно увидеть, работает станок или есть проблемы». Зеленый цвет значка на планшете Андрея означает, что станок работает. Бледно-красный дает понять, что временно остановлен для принятия решения оператором. Более интенсивный красный цвет сигналит – станок стоит более пяти минут и следует немедленно выяснить, почему прервалась работа.
Система позволяет определить, почему неэффективно работает оборудование. Сократили время простоя станков, уменьшили примерно на 20 процентов время подготовки оборудования к работе, а это грамотный подход к планированию работы машинного парка.
Однако в этом автоматизированном царстве нашлось место и ручному труду. Готовые детали доводят до идеала напильниками. И тому есть простое объяснение. После того как деталь сняли со станка, на ней могут остаться заусенцы и их необходимо зачистить.
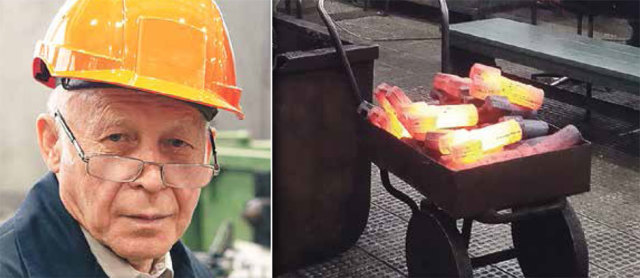
Начальник кузцечного цеха Тафкин Аюпов о своем производстве знает все
Затем – очень сложный предфинишный этап. В светлом электромонтажном цехе под яркими лампами скручивают «нервы» ракеты – на одно изделие приходится более 700 метров проводов.
По словам замначальника цеха по производству Алексея Капкаева, здесь формируют трассы жгута, проводят его распайку, прозвонку, герметизацию и испытания готовой продукции. Сплетенные и спаянные вручную в определенной последовательности провода обрабатывают «химией», затем в специальных печах проводят термообработку. Контакты покрываются специальным герметиком, и после окончательной проверки готовую продукцию передают в сборочный цех.
При этом все работы делаются без какой-либо автоматики. В этом цехе, пожалуй, наиболее высокий процент ручного труда. Пробовали экспериментировать и заменить ручную спайку жгутов автоматической, но после исследования контрольных образцов пришли к выводу, что робот человека здесь заменить не смог.
Трубчатые печи для нефтепровода
Перед сборочным цехом, самым секретным на заводе, – своя проходная и собственная пропускная система. Перед входом нужно предъявить паспорт. На выходе внимательные охранники еще раз сличат фото на документе с оригиналом. Именно тут окончательно собирают ракету и закладывают ее в транспортно-пусковой контейнер. Причем ТПК двух цветов: часть зеленые – для российских подразделений ПВО и песочной расцветки. Эти скорее всего предназначены на экспорт. Рулевой отсек состыковывают с двигательным, затем эту «сцепку» соединяют с агрегатным отсеком, в котором находится бортовая аппаратура управления полетом, наведения на цель и подрыва БЧ.
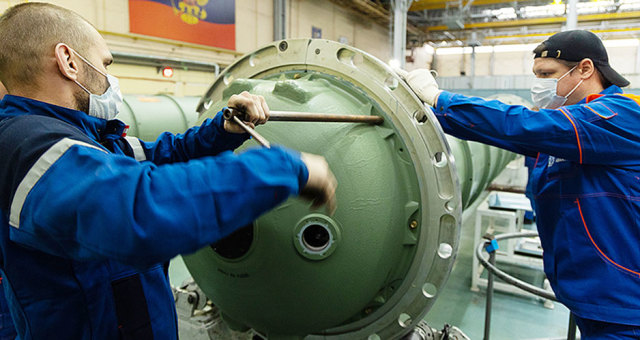
vpk-news.ru
Ракету осторожно укладывают на стапель и медленно и аккуратно заводят в цилиндр ТПК. Сборщики законтрили гайки на крышке контейнера, и после подписания всех документов изделие готово к отправке. Уже далеко от столицы в нее заложат боевую часть, и в этом ТПК оно может храниться годами без потери качества.
Вся аппаратура, которую используют для проверки узлов и систем на этом участке, только отечественная. По словам замначальника сборочного цеха Сергея Григорьева, за рубежом попросту нет приборов, которые могут обеспечить нужный уровень измерений.
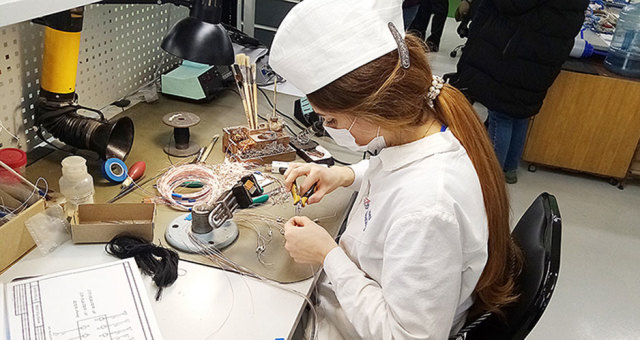
В монтажном цехе женское царство. Фото: Сергей Карпачев
Когда в стране начали говорить о диверсификации оборонных предприятий, на заводе «Авангард» не стали сразу бросаться на поиски свободной ниши на гражданском рынке. При поддержке департамента производственно-технологической политики концерна «Алмаз-Антей», в состав которого завод входит с 2002 года, в 2018-м создали Инновационный центр, в задачах которого – поиск свободных от конкуренции ниш. И уже через год заказчикам поставили первое серийное изделие – трубчатые печи для нагрева нефти на магистральном сибирском нефтепроводе. И это направление продолжает развиваться. Кроме того, сотрудники центра задействованы в реализации гражданского проекта, где предусматривается создание, производство и сервисное обслуживание системы подводной добычи газа. Контракт перспективен для организации работ на шельфе.
«Мы заняли нишу, которую покинули крупнейшие игроки в сфере нефтепереработки, нефтедобычи», – подчеркнул генеральный директор завода «Авангард» Денис Попков.
Сергей Карпачев
Газета "Военно-промышленный курьер", опубликовано в выпуске № 5 (918) за 8 февраля 2022 года