Реформы 90-х загнали в тупик базовую отрасль российской промышленности
В последнее время государство предпринимает определенные шаги для реанимации отечественного станкостроения, однако напомним, что ранее долгие годы делалась ставка на мировой рынок, где Россия будет продавать нефть, а «все остальное» сделают и привезут зарубежные поставщики.
Показательно: в начале 1992 года последний министр станкостроительной и инструментальной промышленности СССР Николай Паничев с трудом пробился на прием к и. о. премьера кабмина РФ Егору Гайдару с детально отработанным планом сохранения отечественного станкостроения. Тот даже смотреть бумаги не стал, брезгливо сморщился: «Да кому нужны ваши дерьмовые станки». И добавил: «Понадобятся – мы все за рубежом купим». Как считал Паничев, это была программа уничтожения отечественной промышленности, перевода России из страны – производителя техники в стан покупателей, что ставило РФ в полную зависимость от Запада. К власти пришли люди, не знающие специфику взаимодействия отраслей промышленности.
Давно известно, что у государства нет будущего, если власть не обеспечивает контур технологической безопасности и независимости. «Рыночники» тогда устремились к приватизации советских предприятий и обеспечению доходов олигархов вместо инвестиций в развитие страны. Наступила эра алчных казнокрадов и разрушителей, менеджеров, почивавших на лаврах сырьевой ренты.
Тупик имени Гайдара
“Если в 1990 году в РСФСР, по данным Росстата, выпускалось 74,2 тысячи металлорежущих станков, в том числе 16,7 тысячи с ЧПУ, то в 2019-м осилили только выпуск 4719 металлорежущих станков (падение в 15 раз)”
В 2014 году Россия вступила в новую фазу противостояния с Западом, замаячила даже новая гонка вооружений. Кризис и санкции изменили ситуацию, правительству пришлось признать, что страна импортирует 90 процентов станков. В тяжелом машиностроении импорт составил 60–80 процентов продукции, в радиоэлектронпроме – 80–90, в фармацевтике и медпромышленности – 70–80 процентов. После падения нефтяных цен и введения западных санкций наступило осознание, что никакие успехи в экспорте зерна, угля, нефти, газа неспособны заменить собственное производство машин, а стратегически техническую независимость обеспечивает станкостроение – основа производства в ключевых секторах: ОПК, авиационной, автомобильной промышленности, тяжелом и энергетическом машиностроении, судостроении и металлургии. К номенклатуре изделий станкостроительных заводов относятся металлорежущие (МРС) и деревообрабатывающие станки, обрабатывающие центры, машины ковочные или штамповочные, молоты, кузнечнопрессовое оборудование (КПО), автоматические и полуавтоматические линии, комплексно-автоматические машиностроительные линии, станки с ЧПУ, литейные машины, режущие, измерительные, абразивные инструменты, оснастка для станков и прочее оборудование. В мире только 34 страны производят станки. После развала СССР в России погибли 44 специализированных предприятия. Станкостроение – сравнительно небольшая по объемам выпуска отрасль и в большинстве развитых стран создает менее 1 процента ВВП. Вклад станкостроителей в ВВП у нас составляет 0,02 процента, что в разы ниже показателей лидеров (Китай – 0,2, Япония – 0,33, Германия – 0,37 процента).
СССР был в тройке мировых лидеров станкостроения с 1938 по 1991 год, а где Россия – наследница СССР находится сейчас?
Кому достался пирог
В 1938 году, когда мир уже предчувствовал Вторую мировую войну, станкостроительных держав было четыре. Лидерами были США и Германия, за ними в четверку входили СССР и Великобритания. В 1970-х годах Великобританию вытеснила Япония. Ситуация за 80 лет значительно поменялась – Штаты сражаются за место в семерке лидеров с Тайванем, поскольку их доля в мировой торговле станками 5–6 процентов, как и Тайваня. России, наследницы СССР, в семерке лидеров нет.
Объем продаж на глобальном рынке, по данным Gardner Research, сегодня превышает 90 миллиардов долларов, при этом темпы прироста мировой станкостроительной отрасли последние 20 лет превышают в среднем 4 процента в год. Для отрасли характерно соотношение, при котором 56,2 процента всей продукции выпускают 3 страны – КНР, Япония, ФРГ. Далее идут США, Корея, Великобритания Франция.
Сегодня основным рынком стал Азиатско-Тихоокеанский регион, считает эксперт Центра развития ВШЭ Александр Бутов. И основную роль играет Китай, с 2002 года мировой лидер потребления станков. С 2009-го на долю Пекина приходилось не менее 33,7 процента от общемирового объема продаж данной товарной группы, а в потреблении станков – до 31,4 процента. Аналитики полагают, что китайский рынок определяет отраслевую динамику в мире.
Второе место в потреблении продукции станкостроения среди макрорегионов удерживает Европа. Причем немецкая промышленность обеспечивает более половины экспорта ЕС за рубеж.
Основной объем мирового рынка станков сосредоточен всего в трех регионах: АТР, Западной Европе и Северной Америке, где ситуация определяется уровнем потребления США.
Лидеры станкостроительной индустрии используют различные инструменты поддержки финансового и нефинансового характера:
- прямое денежное вливание;
- налоговые льготы;
- специальные ставки амортизации;
- льготное долговое финансирование, подготовка кадров и прочие преференции.
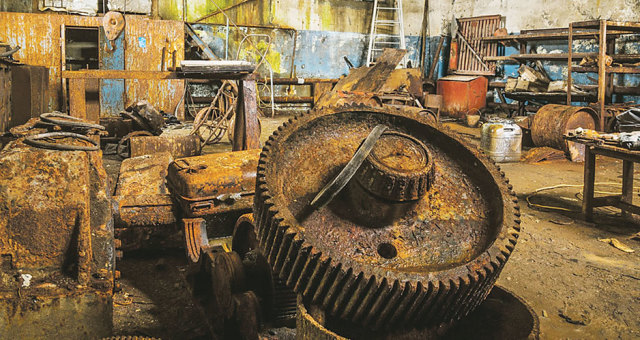
Фото: blogspot.ru
КНР – крупнейший потребитель станков, однако в 2018 году продажи на китайском рынке снизились с 30,7 до 28,8 миллиарда долларов, а доля в мировом потреблении упала до 31,4 процента.
Наиболее передовыми в техническом отношении являются станкостроительные корпорации Trumpf (ФРГ), Amada (Япония), Haas (США). Впереди не только промышленные гиганты вроде Китая и США, но и Австрия, Испания, Бразилия.
Кто станет в будущем абсолютным мировым лидером, сложно определить. В КНР, развивая народное хозяйство, изначально стремились добиться независимости от чужих технологий, и многого достигли. При этом китайцы делают упор на выпуск сложнейших автоматизированных, с компьютеризированным управлением, промышленных станков.
Итак, вместе с Китаем в тройку мировых лидеров производства и экспорта станков входят Япония и ФРГ, далее с отставанием (раза в два) следуют США, Южная Корея, Италия, Тайвань, Швейцария. Доля остальных стран составляет менее одного процента.
Одновременно Пекин, Вашингтон и Берлин возглавляют список не только экспортеров, но и импортеров станков. Ведь при современном производстве узкоспециализированных агрегатов даже для развитой страны рентабельнее купить особо редкие станки за рубежом, нежели тратиться на их разработку и производство. Кроме того, лидеры мирового станкостроения переформатировали отрасль так, что выпуском наукоемких комплектующих занялись локальные центры компетенций. Так, электрошпиндели выпускает одни, револьверные головки – другие, шарико-винтовые передачи – третьи, системы ЧПУ разрабатывают четвертые фирмы. В итоге предприятие на последнем этапе только собирает станок из готовых деталей. Среди поставщиков ЧПУ выделяются страны, традиционно лидирующие в производстве высокотехнологичного оборудования: Япония, ФРГ, США. Российские производители здесь проигрывают в надежности изделий, что ведет к дополнительным издержкам у потребителей наших систем при ремонте и наладке.
В СССР станок не роскошь
В дореволюционной России было примерно 75 000 станков и только 20 процентов – отечественные. Первая мировая и Гражданская войны экономику страны практически разрушили, требовалось восстановление народного хозяйства. В первой советской пятилетке производство станкостроительной продукции росло опережающими темпами.
В 1929 году был образован «Станкотрест». К 1932 году токарные, шлифовальные и фрезерные станки, некоторые другие виды оборудования выпускали восемь специализированных заводов. Накануне Великой Отечественной в СССР работал уже 41 такой завод.
В 1933-м создается экспериментальный НИИ металлорежущих станков (ЭНИМС), ставший научным центром конструирования и исследования данной продукции. К 1940-м годам сложилась научная школа теории механизмов для освоения учеными и инженерами многообразных конструкций сложных по структуре и кинематике машин, станков зарубежного и советского изготовления.
Тогда импорт замещали чрезвычайно успешно: в 1930 году только 34 процента станочного парка было отечественными, а через семь лет этот показатель увеличился до 91 процента. Росло производство сложных и тяжелых станков. Так только на заводах «Главстанкоинструмента» Наркомтяжпрома с 1932 по 1937 год их выпуск увеличился на 84,2 процента. Улучшалось и качество. Простые агрегаты – сверлильные, малые токарные, шепинги изготавливались в артелях промкооперации, ФЗУ, техникумах.
Благодаря успешному развитию отрасли только в 1940 году выпущено 58,4 тысячи станков, а парк металлорежущих станков в СССР составил 710 тысяч единиц. С 1932 по 1940 год парк таких станков в промышленности СССР увеличился в 3,5 раза, а доля специальных составляла 40 процентов в общем производстве.
Немалую роль в развитии советской промышленности, включая оборонную, сыграли закупки в Германии станков и другого заводского оборудования.
Если в 1939 году СССР импортировал из разных стран 3458 станков, то в 1940–1941 годах Берлин поставили 6430 металлорежущих станка на 85,4 миллиона германских марок. Закупленные в те годы новейшие образцы техники и вооружения были с толком использованы советскими инженерами. В СССР германские станки и другое заводское оборудование работали в течение всей войны.
По решению Иосифа Сталина уже в июне 1941-го был создан первый Наркомат станкостроения, который возглавил инженер Александр Илларионович Ефремов, в первые три военных месяца успешно организовавший эвакуацию в Сибирь и на Урал более двух сотен машиностроительных заводов, которые запустили в кратчайшие сроки на полную мощность. В наиболее трудный для страны 1942 год произведено 22 935 металлорежущих станков и 2210 единиц кузнечно-прессового оборудования. В 1945-м производство МРС составило 66, КПО – 62 процента от предвоенного 1940 года, а в 1948-м производственный план был выполнен на 110 процентов.
В послевоенные годы перед станкостроительной отраслью стояли две основные цели – увеличить объем выпуска и улучшить технические характеристики продукции. Введены в эксплуатацию Минский, Рязанский, Коломенский, другие станкостроительные заводы. В СССР производили качественные станки, обеспечивавшие необходимую точность обработки деталей. В 70 годы выпускали около 60 моделей станков с ЧПУ, были созданы предприятия, выпускавшие высокопроизводительные обрабатывающие центры, не уступающие агрегатам европейской выделки. Дополнительно оборудование производилось в странах социалистического лагеря – Чехословакии и Венгрии. В конце 80-х годов СССР вышел на третье место по производству среди станкостроительных держав. Первое место держала Япония, второе – ФРГ, США – четвертые. Союз экспортировал станки не только в развивающиеся страны, но и в Японию, Канаду, США, ФРГ.
Сокращали выпуск устаревших станков, наращивали производство «автоматов». В 1991 году выпустили 76 тысяч МРС и среди них было уже 26 тысяч станков с ЧПУ, 5,5 тысячи обрабатывающих центров и гибких производственных модулей (ГПМ). Они полностью заменили огромный парк универсальных станков. Все промышленные товары, оружие, изделия для покорения космоса выпускались на отечественном оборудовании.
На Ленинградском станкостроительном заводе имени Ильича создали 14 моделей сверхпрецизионных станков, которые и по сей день работают на оборонный комплекс страны. Отрасль развивалась опережающими темпами и в начале 1990-х вышла на мировой рынок, хотя станкостроение на Западе было тогда на подъеме. В 1991 году на Международной выставке станкостроения в Париже были представлены 49 наших машин и станков, которые продали прямо со стендов.
В СССР без импорта и тогда не обходились, но сами производили станки высокого уровня: с 1984 по 1990 год только в ФРГ продали более 45 тысяч станков и кузнечно-прессового оборудования. Японские промышленники ознакомились с оборудованием для безлюдной технологии в СССР на выставке «Станки-72». После компания FANUC в 80 годах организовала в Токио такое первое автоматическое предприятие со станками с ЧПУ и роботами.
А что стало с станкостроением в РФ?
Унылое настоящее
После смены модели экономики в начале 1990-х отрасль оказалась в глубочайшем кризисе, стремительно теряла завоеванные позиции мире. Многие заводы практически полностью остановили производство, другие перестали заниматься разработкой новых моделей оборудования. Ведущие производители разорялись и сворачивали убыточные проекты. Если в 1990 году в РСФСР, по данным Росстата, выпускалось 74,2 тысячи металлорежущих станков, в том числе 16,7 тысячи с ЧПУ, то в 2019-м осилили только выпуск 4719 металлорежущих станков (падение в 15 раз).
Российские производители сегодня занимают менее 10 процентов внутреннего рынка, а производители инструмента для станков – около 40. Сегодня в станкостроении функционирует порядка 80 предприятий, из них 56 производителей МРС, 24 производителя КПО. В производстве инструмента занято 29 предприятий.
Советское станкостроение отличалось широкой сетью специализированных институтов, занимающихся исследованиями и разработками, имелось 44 отраслевых НИИ. Научно-исследовательский экспериментальный институт металлорежущих станков (ЭНИМС), обеспечивавший качественный скачок в промышленности первых пятилеток и в последующие годы, насчитывал 7 тысяч научных сотрудников, а сегодня там осталось меньше сотни немолодых специалистов.
Ныне сохранились три действующих института и организации – МГТУ «Станкин», МГТУ имени Баумана, ОАО «ЭНИМС». Центральным научным отраслевым центром в области инструментальной продукции выступает ОАО «ВНИИИНСТРУМЕНТ» (холдинговая компания АО «Станкоинструмент» ГК «Ростеха»). НИОКР сосредоточены на отдельных кафедрах и центрах. Комплектующее производство представлено 20 предприятиями, но от 40 до 70 процентов в общей стоимости комплектующих для станков составляют импортные компоненты. Кроме того, практически вся отрасль заточена на работу с ОПК и ее продукция незначительно присутствует на гражданском рынке, что надо менять.
Как считают специалисты, основными причинами низкого уровня инновационной активности в станкостроении России являются слабое финансирование отрасли, дефицит квалифицированных кадров, утеря преемственности поколений в НИОКР и производстве, отсутствие системной подготовки кадров для отрасли, сокращение выпускников специализированных кафедр, малый приток молодых специалистов в станкостроение.
Полностью уничтожено 42 станкостроительных предприятия. Среди них Московский станкостроительный завод, Завод имени Орджоникидзе, завод «Фрезер», Завод координатно-расточных станков, Институт ЭНИМС и завод «Станкоконструкция». В Санкт-Петербурге: Завод имени Свердлова – почти половина сделанного на нем оборудования поставлялась на экспорт. Фактически уничтожен Санкт-Петербургский завод прецизионного станкостроения с его уникальным производством. Там создана технология изготовления подшипников и станков для гироскопов, которые используются в авиации, в космосе, для атомных подводных лодок. Такие же подшипники, кроме России, выпускает единственная фирма в мире – американская «Браян». Ни в Европе, ни в Японии их делать не умеют. На наших предприятиях ОПК сейчас уже работает половина систем ЧПУ импортного производства.
Слабый свет надежды
Как считает президент Российской ассоциации производителей станкоинструментальной продукции «Станкоинструмент» Георгий Самодуров, за 25 лет реформ отрасль, как и многие другие, серьезно потрепали, поэтому без трансферта иностранных технологий и помощи от иностранных коллег на данном этапе будет нелегко. Сегодня в отрасли появилось пять групп предприятий.
Первая – иностранные инвесторы. Так в сентябре 2015 года был запущен Ульяновский станкостроительный завод, построенный самым известным в мире концерном ФРГ и Японии DNG MORI и обошлось это иностранным инвесторам в 90 миллионов евро. Трудятся там российские инженеры и специалисты, создано 250 рабочих мест. Локализация производства составляет 50 процентов, производственная мощность –1?200 станков в год.
Вторая – СП, собственниками являются иностранные фирмы совместно с российскими производителями. Их около десяти, это крупные итальянские, немецкие, чешские и швейцарские компании, готовые в ближайшее время создать современные предприятия. Например, в Екатеринбурге создаются СП «EMCO» с «УНИМАТИК», TOS Varnsdorf и «КР-Пром». Процесс идет.
Третья – предприятия станкостроения с вложениями крупных российских инвесторов. В группе «СТАН» объединено пять крупнейших заводов России: НПО «Станкостроение» в Стерлитамаке, «Станкотех» в Коломне, Ивановский завод тяжелого станкостроения, Рязанский станкозавод и Московский завод шлифовальных станков.
Четвертая – традиционные российские производители.
Пятая – крупные дилеры, продавцы иностранного оборудования на российском рынке.
Во время реализации ФЦП «Развитие оборонно-промышленного комплекса Российской Федерации на 2011–2020 годы» осуществлена масштабная модернизация производственных фондов предприятий ОПК, в основном за счет продукции иностранного производства. В Минпромторге не исключают частичное перепрофилирование оборонных предприятий, которые, возможно, займутся изготовлением станков и их комплектующих. В настоящее время предприятия ОПК – основные потребители отечественной станкоинструментальной продукции. Спецификой этого сегмента являются спрос на сложное высокотехнологическое оборудование, а также высокая степень нормативного регулирования закупок. По данным отечественных производителей современного промышленного оборудования, как раз на предприятия ОПК и приходится не менее 80 процентов получаемых ими заказов.
Российское станкостроение пусть понемногу, но возрождается, однако в основном происходит это за счет роста производства станков невысокого уровня использования инновационных технологий, что в импортозамещении прорыва не обеспечит. В итоге сегодня практически вся отрасль заточена на работу с ОПК и незначительно присутствует на гражданском рынке. Для повышения конкурентоспособности отечественной продукции предусмотрено совершенствование существующей системы госрегулирования и поддержки, обеспечение долгосрочного роста производства станков и инструментов со средним темпом на уровне до 5,7 процента в год в 2020–2035-м до уровня 79,5 миллиарда рублей к 2035 году, увеличение уровня локализации российской продукции отрасли до 70 процентов за счет развития отечественного производства ключевых высокотехнологичных комплектующих; обеспечение роста экспорта до 16,5 миллиарда рублей к 2035 году в результате роста технологической и экономической конкурентоспособности российской продукции станкостроения.
Отметим, что технологическое отставание за 10 лет работы в этом направлении частично сократилось, но о полном преодолении говорить пока не приходится.
По заявлению главы Минпромторга РФ Дениса Мантурова, ведомство реализует пакет программ, направленных на содействие замещению импорта. Так, существует подпрограмма «Станкоинструментальная промышленность» государственной программы «Развитие промышленности и повышение ее конкурентоспособности». Документом предусмотрено выделение из федерального бюджета 5 миллиардов рублей на создание опытно-конструкторских разработок, при этом столько же должны вложить и сами промышленники. Однако даже официальные заявления должностных лиц не содержат обещаний о скором восстановлении отрасли.
Так, по словам председателя совета директоров «Станкопрома» Сергея Макарова, на замещение универсального металлорежущего оборудования с ЧПУ, включая многокоординатное, на 70–80 процентов отечественными аналогами, потребуется 5–7 лет. «При этом освоение выпуска всей компонентной базы российского производства потребует значительно большего времени», – считает он.
Николай Домницкий
Газета "Военно-промышленный курьер", опубликовано в выпуске № 36 (899) за 21 сентября 2021 года