Кто обеспечивает выполнение поручения президента России
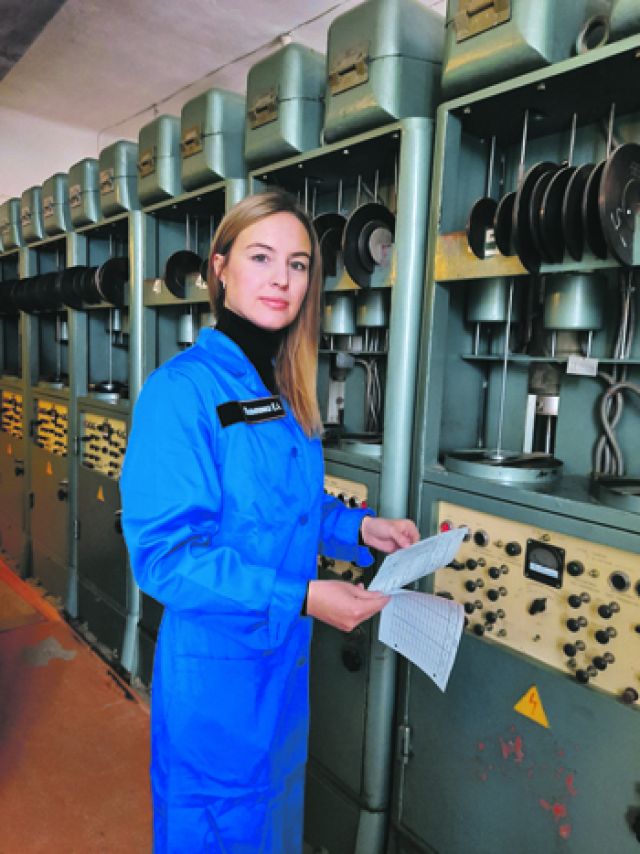
Контроль качества материалов и комплектующих становится главным условием исполнения гособоронзаказа. Фото автора
Доля современных вооружений и техники в 2020 году в Вооруженных силах России достигнет 70%. Эту задачу поставил Владимир Путин. Ее реализация напрямую связана не только с работой крупных оборонно-промышленных концернов, но и с деятельностью поставщиков комплектующих и материалов. Вопрос качества – один из ключевых для выполнения планов. Центр компетенций системы управления качеством госкорпорации «Ростех» (АО «РТ-Техприемка») стал гарантом в проектах, связанных с исполнением государственного оборонного заказа (ГОЗ). Несмотря на кризисное время для российской промышленности, связанное с пандемией коронавируса, приостановкой производства и невозможностью обеспечить плановую поставку необходимых материалов и изделий, компания сумела обеспечить бесперебойную работу технических приемок и региональных технических представительств.
Гарантия обязательств
В начале этого года Центр компетенций системы управления качеством заключил соглашение с Минобороны в области контроля качества. Это позволит решить такие стратегические задачи, как обеспечение прозрачности прохождения материалов, используемых при создании вооружения и военной техники, от изготовителя до производителя, в том числе проверку подлинности сопроводительной документации. Это позволит исключить случаи применения предприятиями промышленности неаутентичной продукции при выполнении ГОЗ. Однако на данный момент существует еще несколько ключевых вопросов, которые требуют решения и обсуждения.
Один из таких вопросов – гарантийные обязательства на поставку комплектующих, которые бывают ниже гарантийного срока, установленного государственным заказчиком на конечное изделие. Этот вопрос несомненно нужно решать в интересах потребителей, которые будут эксплуатировать изделие, а не его комплектующие. Так, осенью 2019 года АО «РТ-Техприемка» увеличило гарантийный срок эксплуатации комплектующих вертолетов Ми-26 и модификаций Ми-8 на 6–12 месяцев, а гарантийный ресурс на 500 часов. Центр качества поставок провел работу по систематизации мер взаимодействия с 11 поставщиками 50 комплектующих изделий. Все эти меры позволят сэкономить средства предприятий – изготовителей конечного продукта, которые они тратят на ремонт и покупку новых комплектующих. Ранее, в 2018 году подобный проект был реализован совместно с Уралвагонзаводом.
Кроме того, сейчас нормативно не урегулирован вопрос ответственности исполнителя, предоставившего некачественный материал. Многие поставщики также не несут ответственность за простой предприятий, производящих оборонную продукцию и исполняющих ГОЗ. Несоблюдение требований Положения об условиях государственных контрактов по ГОЗ позволяет некоторым поставщикам комплектующих снижать свои экономические риски в таких важнейших аспектах, как надежность поставляемых изделий.
Возложение экономической ответственности за надежность поставок комплектующих изделий на соответствующих поставщиков приведет к выполнению мероприятий, направленных на повышение надежности поставляемых изделий.
Военпред на страже качества
Выполнение ГОЗ – сложный процесс, имеющий свои особенности, которые не ограничиваются участием в нем государственного заказчика и исполнителя. В особых случаях он требует привлечения специализированных организаций.
Для борьбы с некачественной продукцией в соответствии с федеральным законом о ГОЗ привлекаются военные представительства Министерства обороны Российской Федерации. Их роль нормативно закреплена в «Положении о военных представительствах Министерства обороны Российской Федерации», утвержденном постановлением правительства Российской Федерации от 11 августа 1995 года № 804.
В целях достижения предприятиями соответствующего качества поставляемой продукции на военные представительства возложены полномочия приостанавливать приемку и отгрузку продукции в следующих случаях: невыполнение условий государственных контрактов; отрицательные результаты испытаний военной продукции; нарушение особо ответственных технологических процессов производства; выявление дефектов в процессе эксплуатации военной продукции, вызывающих ее выход из строя; использование в производстве военной продукции контрафактных, фальсифицированных комплектующих изделий, материалов и полуфабрикатов, а также признание изготавливаемой военной продукции контрафактной.
Такие полномочия военных представительств снижают риски попадания в Вооруженные силы вооружения и военной техники ненадлежащего качества.
Окоп на линии
Специалист технической приемки отвечает за контроль и ведение технологической документации, технологию изготовления подконтрольной продукции, проведение всех видов ее испытаний в соответствии с требованиями документации. Контроль качества изготовления материалов и полуфабрикатов проводится представителями технических приемок непосредственно в цехах, на рабочих местах, на всех стадиях изготовления, включая маркировку, консервацию и упаковку.
В процессе проверок предприятий-изготовителей и предприятий-посредников специалисты технических приемок осуществляют контроль легитимности получения материалов и полуфабрикатов, их дальнейшего использования в системе логистики и возможности применения в производстве на предприятиях-изготовителях. В случае выявления материалов и полуфабрикатов с несоответствующими сопроводительными документами данная продукция должна быть изолирована до выяснения причин несоответствия.
Специфика контроля качества различна для каждого материала и полуфабриката во всех отраслях. В зависимости от различных технологических параметров производства продукции специалистами технических приемок проверяется различный набор показателей.
Для осуществления оценки соответствия оборонной продукции (работ, услуг), включая изделия и их составные части, комплектующие, сырье и материалы, а также оценки соответствия процессов требованиям государственным заказчиком и головным исполнителем привлекаются специализированные организации. Продукция, контролируемая их специалистами, применяется, например, для изготовления основных силовых и особо ответственных элементов конструкции воздушного судна, а также элементов, повреждение которых отрицательно повлияет на его способность функционировать.
Реализация принципа независимости должна осуществляться начальником технической приемки и заключается в разработке и организации им на предприятии-поставщике системы независимого технического контроля производства продукции, поставляемой конечным предприятиям – потребителям изделий авиационной и космической техники, в соответствии с требованиями ГОСТ Р 52745-2007. Важно отметить, что стабильность технологических процессов при производстве материалов и полуфабрикатов играет приоритетную роль в обеспечении их качества (справка).
Любой технологический процесс изготовления материалов и полуфабрикатов имеет множество характеристик, но всегда можно выделить те, которые оказывают значительное влияние на функционирование и качество изготавливаемой продукции. Они называются ключевыми.
Ключевые характеристики технологических процессов на предприятиях-поставщиках, как правило, определяются исходя из опыта сотрудников технологических отделов и указываются в технологической документации. Кроме того, для выявления таких характеристик может использоваться Potential Failure Mode and Effects Analysis (FMEA) – анализ видов и последствий потенциальных отказов.
Примерный показ
Рассмотрим, например, технологический процесс изготовления прессованного профиля из алюминиевого сплава. На этапе «прессование» ключевыми характеристиками являются: температура литой заготовки перед процессом прессования, температура контейнера пресса, скорость прессования. Контроль их соответствия требованиям технологического процесса позволяет исключить появление дефектов (в том числе и скрытых) готовой продукции, например трещин на поверхности изделия, разрывов металла внутри изделия, пережимов, поверхностных пузырей и отслоений.
Наряду с контролем технологических процессов технические представительства и приемки осуществляют контроль соответствия методик проведения контрольных испытаний продукции. Так, если в процессе проведения испытаний ключевые характеристики будут нарушены из-за неисправности испытательного оборудования или невнимательности персонала, то контрольные испытания будут проведены некорректно, а их результаты окажутся недостоверными. Важно также отметить, что контроль соответствия ключевых характеристик требованиям ГОСТ при проведении испытаний позволяет получить истинные значения механических свойств изготовленной продукции.
Для проведения контрольных испытаний от партий материалов и полуфабрикатов отбираются пробы. Места отбора проб определены в нормативной документации. На основании результатов контрольных испытаний служба технического контроля предоставляет предприятию заключение о качестве продукции (заключение о соответствии характеристик материалов и полуфабрикатов требованиям заказчика).
К примеру, если изготавливаемым полуфабрикатом является прессованный профиль из алюминиевого сплава длиной 5 м, то от одного из его концов отбирается проба для проведения контрольных испытаний механических свойств и микроструктуры. По результатам проведенных испытаний дается заключение о качестве всего профиля. При этом предполагается, что такие же механические свойства и микроструктура присутствуют по всей длине профиля (в любом сечении), так как они обеспечиваются технологическим процессом производства. Важно подчеркнуть, что это предположение верно только при условии стабильности (отсутствия нарушений) технологического процесса.
Если в процессе выполнения операции технологического процесса закалки из-за неисправности производственного оборудования или отсутствия надлежащего контроля со стороны производственного персонала температура профиля при нагреве по всей его длине не будет находиться в определенном интервале, то в какой-то его части может появиться участок, механические свойства и микроструктура которого не будут соответствовать требованиям нормативной документации. То есть появится скрытый дефект, который невозможно выявить ни при проведении контрольных испытаний на предприятии-поставщике, ни при проведении входного контроля на предприятии-потребителе, так как места отбора проб на обоих предприятиях идентичны.
Нетрудно представить, какие последствия может повлечь такой скрытый дефект, если профиль используется для изготовления силовых или особо ответственных элементов конструкции воздушного судна или изделия вооружения и военной техники. Силовой элемент конструкции под воздействием нагрузок, возникающих в процессе эксплуатации, может разрушиться, что, в свою очередь, может привести к катастрофе.
Подводя итог, можно сделать вывод о том, что только стабильный, выполненный без нарушений технологический процесс позволяет избежать возникновения дефектов, в том числе и скрытых, и изготавливать материалы и полуфабрикаты надлежащего качества. А значит, обеспечивать стабильно высокое качество продукции гособоронзаказа.
Денис Конончук
Денис Валерьевич Конончук – первый заместитель генерального директора АО «РТ-Техприемка».