В космос приходят интеллектуальные материалы
К материалам, применяемым для создания космических аппаратов, предъявляется целый ряд специальных требований. Есть среди них и совершенно неожиданные, с точки зрения конструкторов наземной техники. Например, устойчивость к испарению. В глубоком вакууме с той или иной скоростью испаряются абсолютно все материалы.
Один из пионеров космического материаловедения – Всероссийский институт авиационных материалов (ВИАМ), основанный в 1932 году. Создавая на первом этапе своей деятельности материалы для авиационной промышленности, институт в начале 50-х подключился к космической тематике. Именно здесь был создан алюминиевый сплав AMг6, который использовали для изготовления первого искусственного спутника Земли, запущенного в 1957 году.
“ Увеличение стабильности покрытий продлит срок службы спутников, находящихся на самых «жестких» орбитах, до 15 лет ”
Сплав уникальный – помимо алюминия, в нем используются еще восемь химических элементов: магний, железо, медь, кремний, бериллий, марганец, титан, цинк. В результате был получен материал, который имеет самый низкий удельный вес среди сплавов алюминия. Существенное достоинство, ведь конструкторы борются за каждый грамм, чтобы облегчить выводимые в космос грузы. Помимо этого, AMг6 является самым прочным и твердым из всех алюминиевых сплавов. Это от него и требовалось, поскольку из-за отсутствия опыта конструкторы стремились сделать шарик с передатчиком внутри таким, чтобы его не разрушили космические микрометеориты. Но при этом сплав получился именно космическим, поскольку в химически активной среде, то есть на Земле, он обладает невысокой устойчивостью к коррозии.
Приложили руку ученые ВИАМа и к созданию ракеты-носителя Р-7. В ее двигателях РД-107 и РД-108 применялись стали, обладающие повышенной жаропрочностью. При этом была решена проблема создания материала для топливных баков, который обладает большой антикоррозийной стойкостью, поскольку должен работать в сильно агрессивной среде жидкого кислорода. Была разработана аустенито-мартенситная сталь марки ЭИ654, легированная кремнием. По словам разработчика двигателей, генерального конструктора академика Валентина Глушко, создание ракетных комплексов было бы невозможным без материалов ВИАМа.
Участвовал ВИАМ и в создании космического корабля «Восток», на котором 12 апреля 1961 года Юрий Гагарин совершил первый в истории человечества полет в космос. Создание корабля стало сложнейшей задачей не только для конструкторов, но и для ученых-материаловедов.
В корабле «Восток» использовались следующие материалы, большая часть которых была создана именно для космических аппаратов:
- алюминиевый сплав AMг6 (в герметичном корпусе спускаемого аппарата и приборном отсеке);
- алюминиевые сплавы AMг2, AMг3 (в трубопроводах);
- алюминиевые сплавы Д16, Д19, АК6, АК8 (в силовых деталях);
- магниевый сплав МА8 (в приборной раме приборного отсека);
- стали марок 12Х18Н10Е, 07Х16Н6, Ст20, Ст45 (для крепежа и силовых деталей);
- титановые сплавы ВТ6, ВТ14 (в шаровых баллонах высокого давления).
Значительные усилия были приложены к созданию теплоизоляционных материалов для спускаемого аппарата, внешняя поверхность которого при вхождении в атмосферу и торможении разогревалась до полутора и более тысяч градусов.
Сотрудники ВИАМа предложили схему термозащиты корабля, которая использовалась не только на «Востоке», но и на последующих космических кораблях. Теплоизоляционный материал АТМ-1 представляет собой экранно-вакуумную конструкцию, в которую входит сотовая структура на основе стекловолокна с размером волокон 2–3 микрометра, пропитанная полимерными связующими. АТМ-1 имеет низкую плотность 10 килограмм на кубический метр. Помимо АТМ-1, в космических аппаратах используется теплозащитное покрытие ВШ-4, которое наносится напылением. Оно создано на основе модифицированных фенолформальдегидных олигомеров и минеральных порошкообразных наполнителей.
Вместе с «ключевыми» материалами на раннем этапе освоения космоса было создано множество клеев, уплотнителей, лаков, эмалей, герметиков, светофильтров, без которых были бы невозможны полеты ни на орбиту, ни к Луне, Венере, Марсу.
Челнок с бразильским песком
ВИАМ активно участвовал в проекте «Буран», в ходе которого было создано более 70 новых материалов и технологий, примененных в многоразовом космическом корабле.
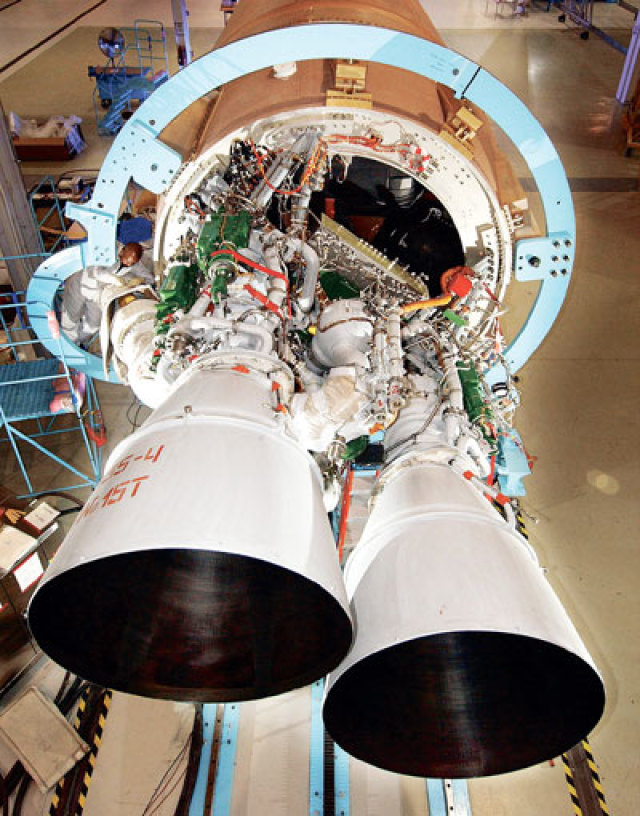
Строительство адронного коллайдера
Фото: thealphacentauri.net
Наиболее сложной в научном и технологическом плане стала разработка теплозащиты челнока. Для носового обтекателя и передней кромки крыла были созданы два жаропрочных композиционных материала на основе углеродной ткани – Гравимол и Гравимол-В. Они с запасом выдерживают температуру 1800 градусов, до которой нагреваются фронтальные элементы «челнока» при вхождении его в атмосферу на гиперзвуковой скорости. Кстати, название материала составлено из первых слогов организаций, его разработавших – НИИ «Графит», ВИАМ, НПО «Молния».
Сам планер спроектирован на работу в температурном диапазоне от минус 150 до плюс 1250 градусов. Это обеспечивается последовательным нанесением на корпус: эпоксикаучуковой грунтовки ЭП-0214, клея-герметика Эластосила 137-175М (разработан ВИАМ совместно с Государственным НИИ химии и технологии элементоорганических соединений), теплозащитных пластин размером 150х150 миллиметров. При этом лишь 10 процентов объема пластин занимают супертонкие кварцевые волокна, а остальное – воздух. Пластины сверху покрывают силикатной эмалью, которая решает три задачи: защищает от проникновения влаги, предотвращает эрозию материалов, переотражает тепловой поток. Снизу к пластине приклеивалась демпфирующая фетровая подкладка.
Теплозащита «Бурана» уникальна не только по техническим характеристикам. Она исключала возможность аварии, в результате которой сгорел американский челнок «Колумбия». Тогда, в 2003 году при старте космического корабля от топливного бака оторвался кусок теплоизоляции и ударил по теплозащитной плитке на крыле «Колумбии». Этот дефект привел к разрушению значительной части теплозащиты при возвращении челнока на землю. В результате перегрева конструкции произошел взрыв.
Теплозащита «Бурана» устроена таким образом, что такого рода дефекты (отрыв одиночных пластин) можно устранять прямо в космосе. На скафандре космонавта располагались два «кармана» с различными химическими веществами. При нажатии на кнопку они смешивались. И космонавт при помощи «шпателя» наносил на дефектное место слой кремнийорганической пасты. Под действием солнечных лучей происходила полимеризация «заплатки».
О том, с каким «всесоюзным размахом» строился «Буран», свидетельствует, например, такая история. При создании теплозащиты необходимо было использовать сверхчистый кварцевый песок. Песок такого качества в Советском Союзе не добывался, и на этапе проведения НИР его приходилось ввозить из Бразилии. Но к моменту подготовки производства челнока Уральское отделение АН СССР открыло Южно-Кыштымское месторождение. И в кратчайшие сроки была развернута добыча нужного для космоса песка.
Сплавы и композиты
Космические аппараты по массе на 90 процентов состоят из различных металлов. Именно поэтому материаловеды уделяют им значительное внимание. Может показаться, что в области металлургии все уже давно известно и разработано. Однако это не так. Постоянно создается что-то с новыми свойствами и качество металлов постепенно возрастает.
К ним, как и к другим материалам, предъявляются повышенные требования по предельным температуре и давлению, вибрационным нагрузкам, радиационной стойкости и защите, устойчивости к микрочастицам, низким температурам, глубокому вакууму, коррозии.
В последнее время значительное внимание стали уделять алюминиевым сплавам, легированным литием и скандием, вместо традиционных добавок никеля. Причем это не сплавы в традиционном понимании, а материалы, полученные по технологии гранулируемой металлургии. В результате удельный вес получаемых материалов уменьшается на 10–30 процентов по отношению к традиционным металлическим сплавам. И повышается до 850–900 градусов предельная рабочая температура.
Суть технологии такова. Вначале приготавливается расплав, соответствующий химической формуле избранного материала. Затем получаются гранулы. Для этого используется либо центробежное распыление заготовок, оплавляемых плазменной дугой, либо распыление расплава сжатыми инертными газами. Далее происходят рассев и сепарация гранул, их дегазация. После чего гранулы засыпаются в герметичные металлические или керамические формы. Затем наступает конечная фаза процесса – изостатическое высокотемпературное прессование в инертной газовой среде, когда давление подается равномерно со всех сторон. При этом величина давления достигает 200 мегапаскалей. После чего детали подвергаются механической обработке.
Исследования с выходом на внедрение технологий в производство проводятся и в области очень перспективных материалов, которые называются интерметаллидами. Они представляют собой соединения двух и более металлов, получаемых при помощи порошковой металлургии. В космосе используются, например, соединения никель-алюминий, титан-алюминий, железо-хром-алюминий. Такие соединения обладают сложной кристаллической структурой, за счет чего возрастают их жаростойкость и жаропрочность (до 1200 градусов), другие полезные свойства. При этом удельный век невелик – 3,7–6,0 г/куб. см.
Наиболее бурно развивающаяся отрасль материаловедения для космоса – это, конечно, синтетические композиты. Направление, к которому ученые только подступаются, – «интеллектуальные» материалы. Их отличительная особенность состоит в способности изменять свойства в зависимости от внешней среды. Более того, в перспективе им намереваются придать такое качество, как способность затормаживать нарастание дефекта, стабилизировать свое состояние в критических зонах.
Научный натиск в этом направлении осуществляется на пути создания термостабилизирующих покрытий. Это очень важно для повышения срока службы космических аппаратов на высоких, геостационарных орбитах, где велико ионизирующее излучение. В результате критического нагревания бортовой электроники, частых циклов резкой смены температуры внутри спутников происходит быстрое старение электронных компонентов. Вначале это дает о себе знать в виде сбоев в работе электронных систем. А в конечном итоге приводит к потере работоспособности.
В идеале от терморегулирующих покрытий требуется поддержание температуры внутри аппарата в довольно узком диапазоне. Для этого они должны отражать поступление внешней тепловой энергии и выводить внутреннюю, чтобы исключить перегрев. Если же температура стремится к своей нижней границе, то отводу тепла необходимо препятствовать. На первых порах существующие терморегулирующие покрытия вполне справляются с возложенными на них задачами. Однако со временем под воздействием ионизирующего излучения космоса терморадиационные характеристики изменяются. Эксперты считают, что с увеличением стабильности и прочих характеристик терморегулирующих покрытий срок службы спутников, находящихся даже на самых «жестких» орбитах, можно довести до 15 лет.
Собственно, чуть ли не у каждого материала, эксплуатируемого в условиях космоса, есть какой-то недостаток, который необходимо свести к минимуму. Это относится и к клеям, которые используются для крепления элементов солнечных батарей, кронштейнов и других деталей. Эпокси-кремнийорганические клеи обладают достаточной ударо- и вибропрочностью, хорошей эластичностью, прекрасно переносят циклические температурные изменения. Но есть и недостаток, довольно существенный – высокое газовыделение (до 8%) при воздействии вакуума. Выделяющиеся газообразные продукты оседают и на пластинах солнечных батарей, и на оптических приборах. Это приводит к ухудшению работы спутников и опять же к сокращению срока их службы. Сейчас химики стараются получить клеи, газовыделение которых не превышает одного процента.
Более легкие и прочные композиционные материалы на основе углепластика и стеклопластика начинают вытеснять металлы из силовых конструкций. У них есть еще одно достоинство – стабильность размеров и объема при изменении температуры во всем рабочем диапазоне. Если для гагаринского корабля «Восток» газовые баллоны делали из титанового сплава, то теперь для этого используются стеклопластики.
Востребованы в современном космическом строительстве и сотовые трехслойные материалы из углепластика. Обладая прекрасной прозрачностью для радиоволн, они широко используются для радиотехнических целей.
Владимир Тучков
Газета "Военно-промышленный курьер", опубликовано в выпуске № 13 (826) за 7 апреля 2020 года