26.11.2018
Внедрение ERP на предприятии. Этап 2 - SCADA
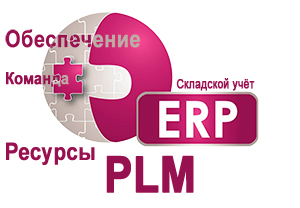
В предыдущей статье мы уже сделали одну обратную интеграцию из ERP в PLM по передаче данных об использовании замен и ненормативного отпуска.
Сам факт возникновения потребности в такой интеграции подталкивает нас к мысли, что разработанные или перенесенные из старых систем технологии не полностью соответствуют реальному производству.
Развивая эту мысль, можно и нужно предположить, что проблемы несоответствия могут быть не только в назначении материалов, но и в маршрутах, и в операциях, и в нормативах, и в самой КД.
Предыдущая статья: Как внедрять ERP. Этап 1 - складской учет.
Многие из перечисленных вопросов можно решить походами в производство, подключением большого числа специалистов из отделов технолога, конструктора и технологов производства для уточнения составов и технологий. При таком подходе, приложив немалые усилия и потратив много человеко-месяцев, Вы сможете получить лишь «выверенные на 80% основные данные по НСИ по состоянию на дату _____».
Понимая это, а возможно уже и пройдя через это, нужно искать инструменты, которые позволят нормативке жить и дышать в системе точно также, и в том же ритме, в каком дышит предприятие. И на рынке есть инструменты, которые позволяют максимально к этому приблизиться. Одним из таких инструментов является – SCADA (Supervisory Control And Data Acquisition — диспетчерское управление и сбор данных), в частности система контроля загрузки оборудования.
Каковы цели?
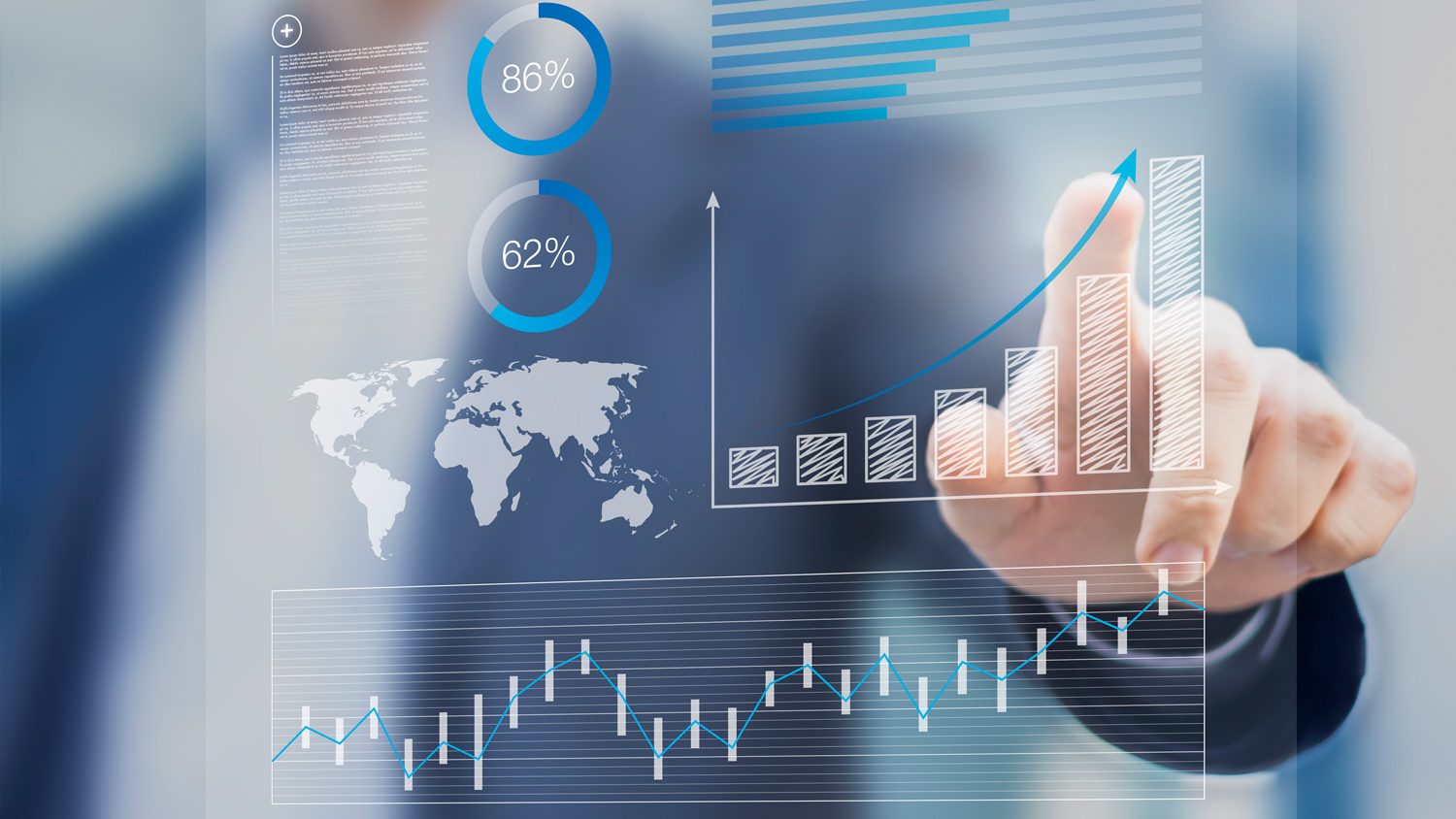
- Подключить в SCADA все станки на одном участке - и ЧПУ, и универсальные.
- Контроль фактической загруженности оборудования.
- Контроль и идентификация простоев.
- Интеграция с PLM по программам ЧПУ.
Что имеем?
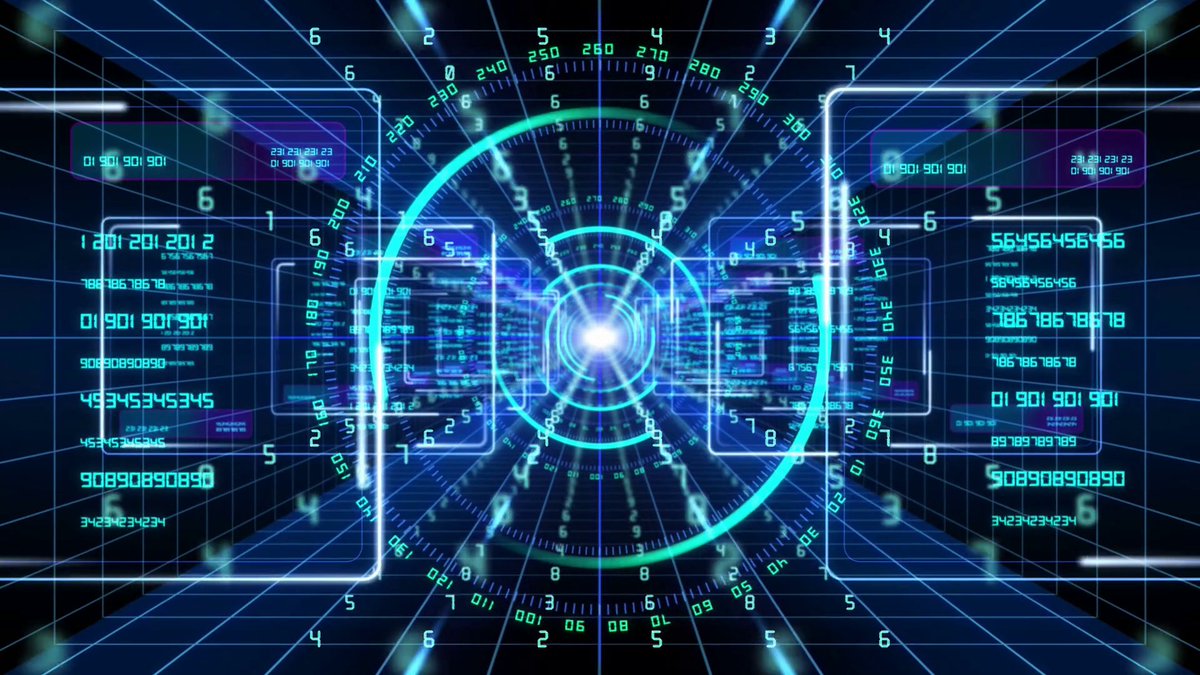
В ERP из PLM оперативно передаются данные по:
- составу изделий;
- структуре производств до участков;
- оборудованию с привязкой к участку;
- пооперационным технологиям с привязкой к оборудованию.
В PLM разработаны и хранятся программы на детали для станков ЧПУ.
Мастер на каждую смену имеет сменное задание с перечнем деталей и количеством к изготовлению. Эту информацию мы получили в ERP в результате внедрения предыдущего этапа (читай предыдущую статью).
Все эти детали к началу смены обеспечены материалами – этого мы тоже достигли на предыдущем этапе (читай предыдущую статью).
Что делаем?
Подключить в SCADA все станки одного участка.
Процесс автоматизации складского учета на всем предприятии является довольно продолжительным по времени, поэтому я бы рекомендовал, начать внедрение SCADA с участка, который попал в первую волну внедрения складского учета.
Выбор системы SCADA является не простой задачей. Поскольку такие системы поддерживают работу с большим числом оборудования и постоянно расширяют этот список, то весь выбор сводится к двум основным параметрам:
- функциональность;
- цена.
Ценовой вопрос в рамках данных материалов рассматривать нет никакого смысла, а вот возможности системы, уже сейчас необходимо рассматривать с учетом создания задела под дальнейшее развитие ERP. Систем класса SCADA на рынке представлено довольно много, есть даже с открытым исходным кодом, однако я попытаюсь показать не системы, а основные функции, которые могут быть востребованы при реализации ERP у Вас:
- контроль работы оборудования;
- контроль простоев оборудования;
- контроль ресурсов узлов;
- контроль параметров работы нагруженных узлов;
- регистрация пользователей – ручной ввод или штрих-коды, или RFID, или голос, или любая биометрия;
- использование программ ЧПУ;
- подсчет числа изготовленных деталей – вручную, автоматически;
- API доступа к данным или отработанная бесшовная интеграция с вашей ERP и вашим PLM;
- развитая визуализация мониторинга состояния оборудования под любую платформу;
- авторизации доступа к интерфейсам;
- полноценные клиентские места по администрированию системы и управления данными;
- хранение данных на СУБД, соответствующей вашей ERP.
Курсивом в перечислении выделил пункты, которые будут нужны Вам уже на данном этапе реализации. Однако, поскольку цикл статей о внедрении ERP, а не SCADA, то сам процесс развертывания системы мы опустим.
Результат подпункта.
Будем считать, что система развернута на выбранном оборудовании.
Контроль фактической загруженности оборудования.

Для обеспечения контроля загруженности оборудования у нас собственно всё есть в SCADA – развернутая система отчетности, показывающая и текущее состояние станка, и динамику за любой диапазон времени в течение смены или заданного периода.
Остается только дать доступ к этой информации в режиме on-line:
- технологам производства, технологам предприятия и БТиЗ производства;
- мастеру, начальнику участка, начальнику цеха;
- службе механика в производстве и на предприятии;
- службе энергетика в производстве и на предприятии.
Задачей мастера и начальника участка является дозагрузка до максимально возможных, принятых для себя, показателей загрузки (рекомендованные значения на данном этапе 60-75%) и при этом максимальное выравнивание этой нагрузки по оборудованию. При попытке выполнить оба условия у Вас, скорее всего, будут выявлены узкие места - единицы оборудования с пиковой загрузкой и явно недозагруженные без возможности их замены каким-либо иным оборудованием из числа имеющегося. Все пытки дозагрузить такие единицы или снять пиковую нагрузку ведут к снижению объемов сменного выпуска или ломке партий передачи деталей между станками.
И это первый повод обратиться к технологам с тем, чтобы они посмотрели на технологию и попытались помочь в решении данной задачи. Здесь подключаться и технологи производства и технологи предприятия.
На задачу необходимо смотреть при разных параметрах сменных заданий – влияние структуры сменного плана на загрузку наиболее критично.
Результат подпункта.
Фактическая загрузка оборудования контролируется в on-line режиме.
Контроль и идентификация простоев.

При попытке дозагрузки оборудования наиболее остро встает вопрос сокращения времени простоя, потому что увеличить загрузку можно только сократив именно это время.
Способов сокращения простоя существует очень много, однако прежде, чем выбрать способ, необходимо понять причины, а в их числе окажутся и весьма объективные – необходимые для производственного процесса простои – например переналадка под другую деталь сменного задания или поднастройка под уже изготавливаемую деталь с учетом износа инструмента.
Каким бы ни был простой, Вам придется потратить время на:
- выявление всех причин простоев, присущих Вашему участку и занесению их в справочники SCADA;
- сбору статистических данных по станкам участка о времени простоя каждого типа на каждом станке.
Без этой работы Вам не будет понятно, с чем надо бороться – с перекурами или оптимизацией числа переналадок в смене.
Если борьбу с перекурами можно отнести чисто к внутренним организационным мероприятиям, то вопросы оптимизации переналадки достаточно многогранны:
- сокращение числа переналадок в течение 1-5 смен, путем склеивания потребностей одной номенклатуры со смещением по срокам;
- оптимизация самой процедуры переналадки;
- подготовка и обеспечение СТО под переналадку.
Еще одним видом простоя оборудования является время на ТО и ремонт. Это очень широкая тема, которая будет затронута позже, однако уже на данной стадии, к работам с данными SCADA необходимо привлечь и механика, и энергетика, не только для анализа частоты простоев по поломкам, но и:
- сбора данных о причинах поломок;
- более глубокого знакомства с возможностями SCADA по считываемым параметрам со станков.
Эти данные, в будущем помогут механику и энергетику очень серьезно поработать и оптимизировать свои планы по плановому и капитальному ремонту оборудования, а технологам – дадут много пищи, для оптимизации режимов обработки деталей.
Результат подпункта.
Простои контролируются, идентифицированы, выявлены систематические простои:
- непроизводственного характера (устранимые или оптимизируемые);
- производственного характера (неустранимые, но оптимизируемые).
Службы механика и энергетика в режиме on-line могут получать данные об аварийном останове оборудования, а также начали сбор статистики и анализ данных для подготовки к проекту ТОиР.
Отвлечение – аудит оборудования.

Одним из побочных, но очень существенных шагов при реализации данного этапа является проведение полного аудита станочного парка, по всем параметрам. Эта работа не будет являться целью, но станет необходимой для того, чтобы:
- оценить какую максимальную загрузку может выдержать конкретная единица оборудования;
- какой ремонт и на какой период необходимо запланировать для конкретной единицы оборудования, чтобы можно было выводить её на максимально возможную для неё норму загрузки.
Интеграция с PLM по программам ЧПУ.
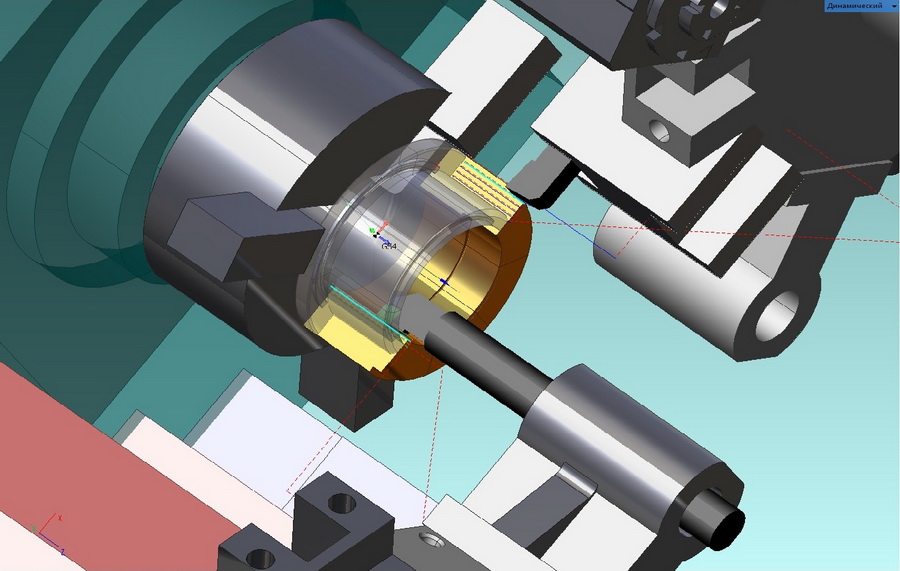
Большинство программ SCADA либо умеют сами хранить программы ЧПУ в привязке к детале-операциям, либо имеют механизмы интеграции, позволяющие своевременно подгружать необходимые программы на станок для выполнения задания.
Вам необходимо выбрать способ взаимодействия между PLM-SCADA по использованию программ ЧПУ и внедрить такое взаимодействие. Необходимо добиться того, чтобы программы обязательно выкладывались в PLM, который должен стать единственным эталонным хранилищем.
Почему это так важно! Системы класса SCADA способны самостоятельно считать количество обработанных на станке деталей по определенным операциям (группе операций). В дальнейшем, для ERP это будет очень важно и полезно – именно автоматический подсчет, без участия человека.
Способов такого подсчета у систем насчитывается целых три:
- по параметрам программы ЧПУ;
- по профилю нагрузки при выполнении операции, группы операций;
- по нагрузке на шпиндель (рабочие механизмы).
Ни один из приведенных способов не идеален в целом, однако может дать результат на определенном сегменте оборудования.
Подсчет деталей по:
- параметрам программы ЧПУ не применим для универсальных станков и требует написания программ специализированных под оборудование, зато является самым точным для ЧПУ, и не требует для этого человеческого участия;
- профилю нагрузки требует замеров профиля под определенный инструмент (набор инструментов, с учетом замен), ведения базы профилей для каждого станка, постоянной их верификации с учетом износа оборудования, при этом имеет нарастающую погрешность при износе инструмента, однако является наиболее точным для подсчета деталей на универсальных станках;
- по нагрузке на шпиндель (рабочие механизмы) не требует никаких замеров или написания каких-либо программ, может применяться для любого оборудования, однако имеет самую большую погрешность в подсчете изготовленных ДСЕ.
Как видим, при наличии программ ЧПУ просто грех ими не воспользоваться в полной мере. Однако, помимо прямой интеграции PLM-SCADA Вам необходимо будет организовать и обратную.
Производство часто сталкивается с проблемами, которых, казалось бы, можно было избежать, но, это только теория. Например у Вас может не оказаться на складе именно такого инструмента, который предусмотрен программой, ну сверло есть только на 2 мм. длиннее, однако – это требует внесения изменения в ПО на деталь. По мере износа инструмента также требуется внесения изменения в ПО, чтобы нивелировать влияние износа, который уже дает результат на границе допусков.
Получается, что необходимо механизм прямой загрузки ПО для ЧПУ на деталь в SCADA, а чтобы получить данные об использовании измененной программы, нужно создать обратную интеграцию, позволяющую передать в PLM:
- обновленную программу ЧПУ в привязке к ДСЕ-операция или программе, которая была обновлена и пришла в SCADA из PLM;
- с какой по числу ДСЕ потребовалось обновление ПО;
- по какой причине – из-за какого инструмента.
Это позволит в PLM:
- сохранить единство первичного архива программ для станков ЧПУ;
- оптимизировать программу с учетом наиболее часто закупаемого инструмента;
- оптимизировать режимы для повышения стойкости инструмента при сохранении качества обработки.
Если на нашем производстве все станки – станки ЧПУ, это безусловный плюс для дальнейшей работы, контроля хода изготовления, оптимизации технологий и норм.
Если же среди нашего оборудования, подключенного к SCADA, есть и универсальное, то какой бы механизм подсчета количества деталей мы не выбрали, помимо него мы получаем фактическое время на выполнении операции на ДСЕ.
Такие данные, накапливающиеся в SCADA или передаваемые в PLM представляют собой качественную статистическую выборку, позволяющую проводить корректировки норм выполнения операций постепенно приближаясь к совпадению с фактическим временем.
Результат подпункта.
Осуществлена интеграция PLM-SCADA по передаче программ ЧПУ.
Осуществлена интеграция SCADA-PLM по передаче:
- измененных программ ЧПУ;
- причинах изменений;
- моменте изменений – ДСЕ-операция, на каком количестве.
SCADA автоматически подсчитывает количество ДСЕ-операций, которые были выполнены на конкретной единице оборудования в течение смены.
Технологи и БТиЗ получают накапливающиеся статистические данные для оценки необходимости корректировки норм или анализа причин отклонения между фактическим временем выполнения операций и нормативным, из PLM.
Что дальше по SCADA.
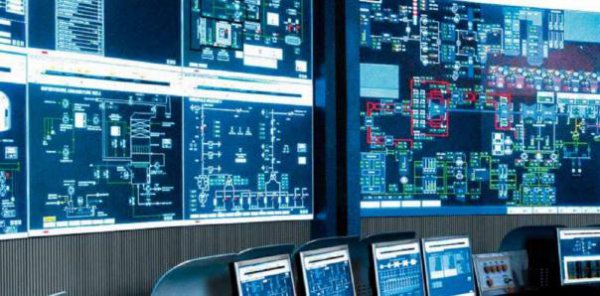
Дальше масштабирование решения сначала по всем участкам производства, затем по всем производствам.
Систематическое расширение справочников с типами простоев, причинами обновления программ ЧПУ и типами поломок оборудования.
Сбор данных по загрузке оборудования и скорее всего – пересмотр кооперации для равномерной загрузки на уровне производств.
С учетом того, что покупка оборудования – очень дорогостоящий проект, имеет смысл уже на данном этапе регулярно проводить верификацию инвестиционных проектов по приобретению оборудования, на предмет фактической потребности в таком оборудовании с учетом открывшихся возможностей анализа загруженности станков по всему предприятию и изменению кооперационных связей, между участками, цехами, производствами и производственными площадками.
Следующая статья: Внедрение ERP на предприятии. Этап 3 – сменное задание из ERP в SCADA.
Автор: Андрей Лабутин