16.12.2018
НЗП и ДПЦ при внедрении ERP на предприятии.
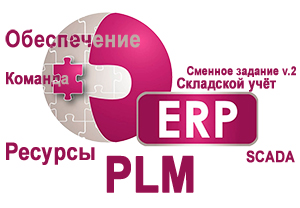
Предыдущие этапы внедрения ERP подготовили хорошую почву для следующего шага – контроля движения деталей и незавершенного производства. Однако, даже имея всё необходимое – до перехода к этапу контроля придется дозревать.
Все предыдущие этапы мы могли начинать опытную эксплуатацию реализации в ERP на отдельно взятом участке и потом масштабировать это решение, параллельно его совершенствуя.
Предыдущая статья: Внедрение ERP на предприятии. Этап 3 – сменное задание из ERP в SCADA.
При попытке контроля движения ДСЕ в масштабе участка Вы сможете увидеть только движение по контрольным операциям и не более того. Задаче контроля НЗП нужен масштаб – передача и получение со складов ДСЕ, перемещение между участками, цехами и производствами. Здесь именно и только масштаб покажет реальный набор проблем, которые надо решить, чтобы физическое движение ДСЕ по предприятию своевременно и достоверно отражалось в ERP.
Ежедневное, а точнее – ежесменное получение такой информации возможно только при наличии контроля движения ДСЕ по всей цепочке изготовления.
Каковы цели?

- Разместить ИТ оборудование для ввода данных в ERP.
- Определить правила контроля НЗП.
- Обеспечить контроль движения ДСЕ в ERP.
- Ввести количественный контроль НЗП.
- Запустить процесс совершенствования ДПЦ.
Что имеем?
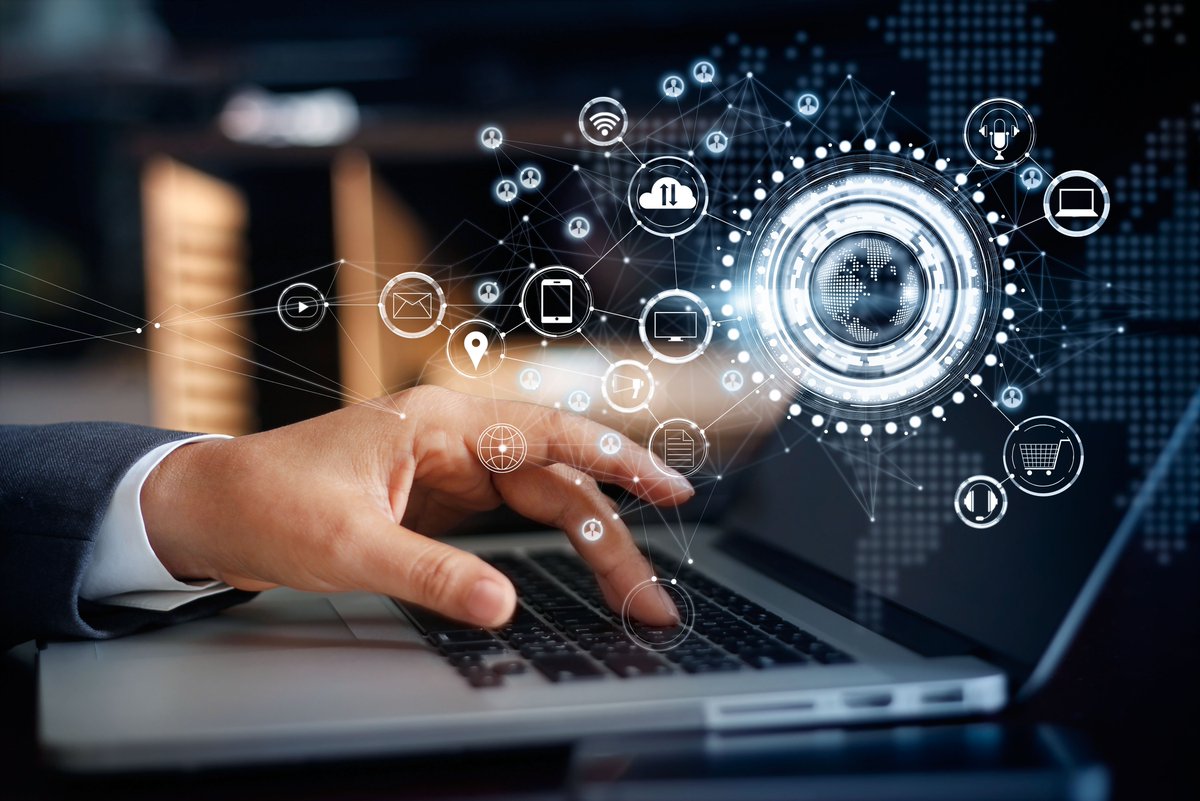
В ERP:
- НСИ изготовления ДСЕ;
- учет движения МКИ и ДСЕ на складах;
- набор контрольных операций выполнения ДСЕ, подлежащих вводу в ERP по факту их исполнения;
- созданы роли для выполнения функций ввода и контроля данных по выполнению ДСЕ в производствах;
- настроены базовые параметры оценки движения ДСЕ – сменность, партии передачи;
- закреплены специалисты по вводу данных, обучены и им предоставлен доступ;
- сменное задание обеспеченное МКИ и/или ДСЕ с привязкой к станку.
В SCADA:
- программы на операции с ДСЕ для станков ЧПУ;
- сменное задание из ERP;
- подсчет количества изготовленных ДСЕ (на станках ЧПУ).
На реальном производстве:
- выделенные места размещения ИТ оборудования ввода-вывода данных в/из ERP;
- изготовлена, закреплена за рабочим пространством и размещена на местах тара для накопления и перемещения ДСЕ между оборудованием.
Что делаем?
Разместить ИТ оборудование для ввода данных в ERP.
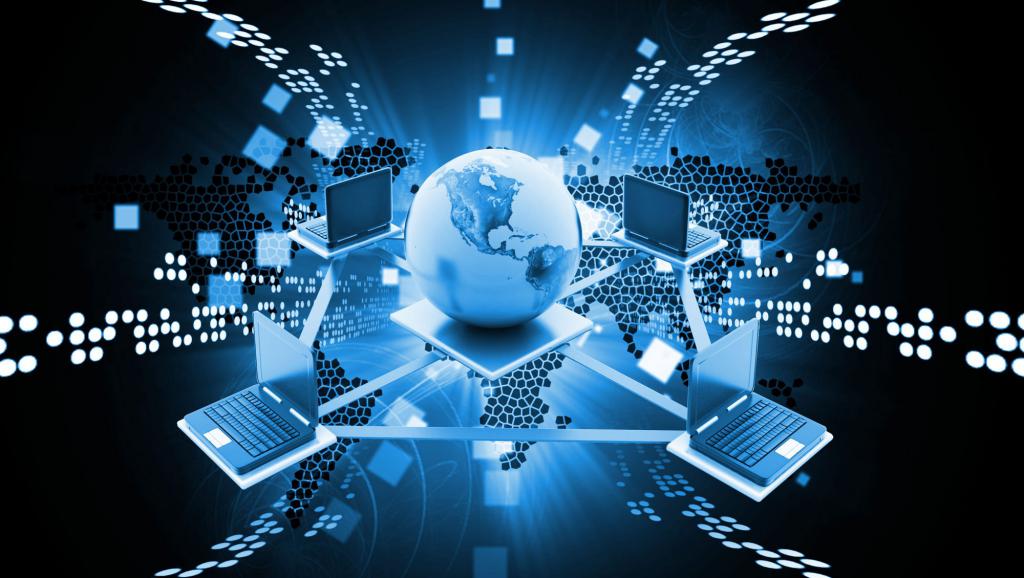
Прошлый этап внедрения мы завершили утверждением планировок с нанесенными точками размещения ИТ оборудования для ввода данных в ERP об изготовленных ДСЕ.
Как, сколько и какое будет размещаться оборудование, зависит от того, какие решения вы принимали на предыдущих этапах внедрения системы.
ВАЖНО. Это выражение «зависит от того, какие решения вы принимали на предыдущих этапах», обозначающее зависимость текущих решений от ранее принятых или будущих ограничений от решений, которые вы принимаете сейчас, я укажу именно здесь, НО – практически все дальнейшие этапы внедрения эта фраза или мысль будет преследовать Вас на каждом шагу. Принимая какое то решение здесь и сейчас, и неизбежно находясь в ограниченных ресурсах, считайте не только текущий показатель результат к затратам, но и вероятность роста или переноса затрат по проекту на будущие периоды от принимаемого решения, а также снижение эффективности текущих и будущих решений в угоду выполнению других текущих показателей.
Итак, у Вас был выбор:
- на какое оборудование ставить SCADA, а на какое нет;
- сколько сделать точек контроля движения ДСЕ для ERP.
И вот в зависимости от того, какие решения вы принимали тогда, сейчас вы будете формировать точки ввода.
Чтобы стало очевидным, что я имею ввиду, здесь, я опишу эти зависимости, надеясь на то, что в будущих статьях мы будем их выявлять в дискуссиях.
Если Вы поставили SCADA только на ЧПУ, то автоматический подсчет деталей вы сможете получать только с них, а следовательно только рабочие с этих станков не должны будут самостоятельно вводить данные о сделанных деталях с применением какого-то дополнительного ИТ оборудования.
Если Вы не стали себя утруждать большим числом точек контроля состояния изготовления ДСЕ для ERP, то мест ввода этих данных будет мало, правда и контроль будет слабее, НО – мы сейчас рассматриваем вопрос именно влияния на число единиц ИТ оборудования и точек ввода. И в данном случае зависимость просто прямая.
Мне понятно, что те или иные решения, иногда даже снижающие точность, появляются из-за финансовых ресурсов или недостаточной заинтересованности принимающих решения, но всё же – риски, закладываемые такими решениями, должны быть как минимум осознанными.
Что касается ИТ оборудования, то здесь тоже существует немало подходов и каждый из них уже доказал свое право на жизнь, работая на различных предприятиях:
- К каждому станку, где нет автоматического подсчета деталей, и у каждого сотрудника, закрепленного за ввод данных в ERP, если это не рабочий у станка, на рабочем месте монтируется небольшой держатель для планшета или специального защищенного устройства ввода и вывода информации, для того, чтобы сотрудник мог максимально оперативно указать количество годных (бракованных – в зависимости от функции сотрудника) деталей, которые прошли через него по маршруту изготовления. Самый дорогой и эффективный способ обеспечения контроля.
- Для каждых N мест устанавливается совместный терминал (экран или киоск, или обычный ПК) ввода и вывода информации, для того, чтобы рабочие, закрепленные за вводом на данном терминале с определенной периодичностью, установленной внутренним распорядком, подходили к терминалу и осуществляли ввод выполненных объемов по каждой ДСЕ. Средняя стоимость при высокой эффективности обеспечения контроля.
- За каждым участком закреплены люди, осуществляющие ввод данных в ERP по информации рабочих или мастеров. Сидеть эти люди могут где угодно, а оперативность попадания данных в систему определяется в этом случае чаще всего двумя параметрами – удаленностью этих людей от участка и частотой выпуска деталей с участка. Самая низкая стоимость реализации и самый низкий уровень достоверности и оперативности контроля.
По жизни, мне встречались все подходы, начиная с планшета ввода на каждом станке, до банального старенького ПК стоящего где-то у плановиков на другом этаже, и даже в другом здании. Встречались и смешанные схемы.
Выбор варианта, как всегда за вами – вопрос более чем не простой, но самое приятное, что при необходимости, в будущем, всё можно докупить и поставить, если позволяет пространство на участках.
Результат подпункта.
Развернута ИТ инфраструктура для ввода информации в информационные системы.
Определить правила контроля НЗП.

Существует два подхода к выбору точек контроля состояния НЗП:
- на складах ДСЕ;
- по фактическому нахождению ДСЕ.
Учет НЗП по складам ДСЕ основан на принципе учета только тех ДСЕ, которые к моменту контроля находятся на виртуальном складе ДСЕ в ERP. На практике этот подход мне встречался в двух вариантах.
Вариант 1 - дискретные проверки.
Ряд компаний на разных стадиях развития или внедрения ведут учет НЗП дискретно по времени, например – раз в неделю, или раз в месяц, реже – раз в день. При таком контроле ко времени проверки во всех производствах осуществляется максимальная сдача ДСЕ на склады ДСЕ с операций, на которых они находились, независимо от стадии готовности, исключая только состояние заготовок (если последние по технологии не выделены в самостоятельные ДСЕ).
После проверки ДСЕ возвращаются на операции, с которых были изъяты для контроля.
У данной схемы есть только один, но очень весомый плюс – дисциплина. Этот подход заставляет всех провести проверку при каждой сдачи, по сути, полный аудит.
Однако минусов у этой схемы значительно больше, начиная с необходимости создания кучи ненужных накладных на сдачу и выдачу ДСЕ, и заканчивая необходимостью доработок стандартной складской функциональности любой ERP по управлению складом, вводом дополнительных полей по связи ДСЕ с операцией, с которой его сюда положили, чтобы потом знать - куда вернуть. Ну и вы наверное догадываетесь, почему ежедневный контроль при таком подходе крайне редок – ежедневные затраты перевод ДСЕ на склад и обратно в производство становятся просто неподъемны и по времени, и по деньгам.
Вариант 2 – осознанная недооценка.
Учитываются детали, которые находятся в любой момент времени на виртуальном складе ДСЕ в ERP.
Принцип тот же, контроль только того, что на складах ДСЕ, но концепция меняется радикально – проверку можно осуществлять в любой момент времени, т.е. on-line.
При этом, необходимо понимать, что на складах ДСЕ в любой момент времени находятся только полностью готовые ДСЕ или ДСЕ, по которым закончены все операции на данном участке и они ещё не переведены на следующий этап работ по маршруту.
В итоге – из учета выпадают все ДСЕ, находящиеся в любой времени на операциях в производстве.
Оба варианта имеют право на жизнь в разных типах производства и при разных циклах изготовления. Скажем, при единичном производстве мы вполне можем воспользоваться вариантом 1 с нужной дискретностью по времени, и это даст нам полное понимание происходящего, без особых трудозатрат и с малым числом лишних бумаг, хотя и не без них.
При мелкосерийном производстве с очень короткими циклами нам вполне может подойти вариант 2.
Отмечу, что способ контроля НЗП по складам ДСЕ является довольно неточным и не имеет перспективы или, как говорят, задела к модернизации или совершенствованию – стремления к уточнению.
Метод контроля НЗП по месту фактического нахождения ДСЕ в ERP лишен всех этих недостатков и позволяет получить максимально точные данные по НЗП в любой момент времени.
В тоже время данный метод требует не только дисциплины и оперативности ввода информации в ERP, но и большего числа участников, и куда большего количества ИТ оборудования - а это деньги и время.
Необходимо отметить, что именно метод контроля НЗП по месту фактического нахождения ДСЕ позволяет системе развиваться и совершенствоваться дальше. Именно этот метод имеет задел совершенствования учета за счет повышения оперативности и норм, расширения ИТ инфраструктуры и дробления точек контроля на ещё более мелкие, вплоть до каждой интересующей операции, что в итоге может дать тотальный поминутный контроль движения - потоковый график выполнения.
Это очень серьезный и качественный уровень контроля НЗП и производства в целом, включая (в будущем) затраты – на такой информации сам Бог велел не совершать ошибок при принятии решений. ОДНАКО – за всю свою рабочую жизнь в ИТ, я не встречал ни одного примера, где предприятие дошло бы такого уровня контроля, и даже более того – имело бы потребность в такой оперативности для управления.
И снова выбор варианта остается за Вами, моя рекомендация очевидна – по фактическому месту нахождения ДСЕ. Именно к этой цели необходимо идти.
Результат подпункта.
Выбран вариант контроля НЗП, разработан и утвержден на уровне предприятия регламент контроля НЗП.
Обеспечить контроль движения ДСЕ в ERP.

Момент пуска задач после длительной подготовки этого события всегда волнителен. И вроде бы ничего не произошло, просто в какой-то день всем сотрудникам, которые вовлечены в процесс, как минимум сразу на всем производстве скажут «с сегодняшнего дня, каждый из вас осуществляет ввод данных через устройства, за которыми Вы закреплены так, как Вас учили на курсах по работе в системе».
После этих слов, в системе начнутся отметки о выполнении ДСЕ и… повылезают все нестыковки, которые сложатся из:
- НСИ по составу, операциям и маршруту;
- сменных заданий мастеров разных участков;
- ожиданий у общих терминалов или киосков ввода из-за нестыковок по времени между рабочими;
- показанного реального объема годных ДСЕ.
Всё это в купе приведет к необходимости увеличения числа оперативных совещаний в производстве по устранению технических, организационных недоработок и ошибок в данных.
Наиболее остро встанут вопросы:
- согласованности действий мастеров по формированию и исполнению сменных заданий;
- наглядной разницы в производительности разных рабочих.
Отступление - сопротивление.

В этот момент рабочие окажут максимальное сопротивление, вплоть до вывода из строя ИТ оборудования. Вся предварительная подготовка рабочих и рассказы им о «благом деле для предприятия» по факту – будут восприняты ими как «чистое зло» и «тотальный незаконный контроль».
Почему именно сейчас?
До момента запуска это кажется всем какой-то игрой, которая может и не случиться или будет работать совсем не так, как рассказывают. И вдруг… вот оно – пришло лично ко мне и возможности что-то изменить уже нет никакой, кроме … - тут у кого на что хватит деструктивной фантазии.
Cразу после запуска будет видна производительность каждого рабочего, как минимум на уровне смены, а поскольку в любой системе оплаты труда прямо или косвенно заложен KPI выполнения плана во времени, то всё это неминуемо отрицательно скажется на заработной плате тех, кто делает медленно и некачественно, и, первое время, никак не скажется на заработной плате тех, кто делает хорошо и быстро. Таким образом – недовольны будут все.
Добавим к этому ошибки системы, которые могут не позволить рабочим проводить свои отметки быстро и без проблем, заявления вышестоящего руководства о том, что они (рабочие) делали не то, что нужно из-за несогласованности действий мастеров смежных участков и… мы получаем почти революционную ситуацию.
Через это проходят почти все. Это плохо, но неизбежно!
Постарайтесь активировать командную работу https://vpk.name/blog/erp-promyshlennost-shag-1--recource, чтобы «невзгоды» легли на плечи всех участников процесса, ни в коем случае не абстрагируйтесь от процесса.
Всё идет по плану.
---
Если ситуация будет накалена до предела, то получая информацию о реальном состоянии дел по каждому рабочему, можно не применять данных KPI к заработной плате рабочих, а только проводить разъяснительную работу с ними через мастеров, показывая им наглядно, что идет не так и выясняя причины происходящего.
На данном этапе – это вполне допустимо, поскольку пока мы не добрались до затрат и оценки НЗП, мы запустили процесс только для получения реального движения ШТУК.
Это ослабит накал страстей, но для проекта это будет не очень хорошо и вскоре Вам всё равно придется вернуться к вопросам стимулирования дисциплины и производительности именно через оплату труда.
Согласованность по стыковке планов – не менее серьезная проблема, чем возмущенные рабочие. Поскольку на данном этапе в системе отсутствует производственное планирование, Вы ничем не можете помочь мастерам в составлении сменных заданий, кроме советов – всё, что можно было автоматизировать на данном этапе по рутинным операциям, Вы к данной стадии реализации, уже сделали.
Основное направление согласованности, которое может дать хороший результат – идти в сменных заданиях с конца цепочки изготовления в производстве. Мастер последнего звена изготовления, помимо формирования суточного задания на следующую смену должен сформировать и дефицитку на ДСЕ через смену.
Практически на всех производствах, где я был – дефицитка, как документ у мастеров присутствует и без ERP, и даже там, где уже есть ERP, и даже там, где в ERP уже работает планирование, а у многих даже в ERP. Поэтому для мастеров это не станет чем-то неизвестным, непонятным и не будет воспринято, как новая работа (дополнительная нагрузка). Другой вопрос, что в предложенных условиях – содержимое дефицитки может претерпеть изменения.
Дефицитка по ДСЕ станет основой для всех мастеров ниже (раньше) по маршруту изготовления при формировании своих сменных заданий на следующую смену, что, в общем, скорее всего работало и до этого.
Конечно, я описываю почти идеальную ситуацию, когда циклы по маршруту у всех не превышают смены, однако более длинные циклы не изменят принципов формирования дефициток, а лишь потребуют создания их на период длиннее циклов, затронутых в дефицитке ДСЕ. В идеале дефицитка должна иметь всего три значения – ДСЕ, дата сдачи на конкретный склад участка мастера, составляющего дефицитку, минимальное количество к сдаче в указанный срок.
Не спешите автоматизировать дефицитку и вообще вносить её в систему. Пока «вылизывается» процесс согласования между мастерами форма, содержимое и принципы формирования дефицитки много раз поменяются.
Ваша задача не терять этот процесс из вида ни на одну смену. Вы должны отследить и записать весь процесс логических выкладок при совершенствовании этого промежуточного документа. Вам будут важны все идеи, включая те, которые по тем или иным причинам не прошли, или умерли в процессе «эволюции» дефицитки.
Имея на руках такую аналитику рассуждений, возможно уже на стадии урегулирования процесса согласования сменных заданий между мастерами, Вы сможете помочь им какой-то долей автоматизации, НО в будущем Вам очень пригодиться этот документ.
Результат подпункта.
Запущено движение ДСЕ по производству.
Получены данные о реальном:
- состоянии НЗП в любой момент времени;
- движении годных и негодных деталей;
- производительности каждого рабочего.
Ввести количественный контроль НЗП.
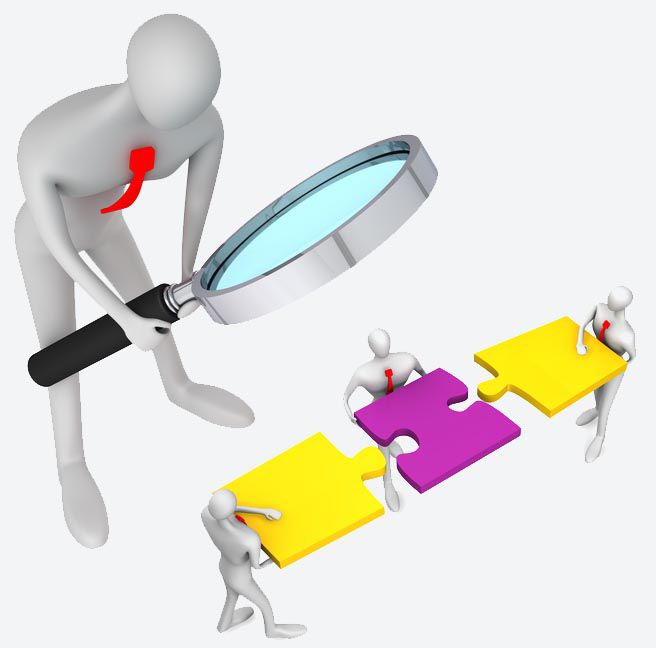
Движение ДСЕ приводит к тому, что мы можем видеть состояние НЗП в дискретном режиме или on-line, в зависимости от реализации, ОДНАКО – видеть и контролировать, это два разных состояния.
Для наглядности состояний приведу аналогию - ваш маленький ребенок скатывается с горки и вы:
- наблюдаете за этим сидя рядом на лавочке – в режиме on-line;
- стоите около горки готовые подстраховать или поймать его в любой момент, если что-то пойдет не так.
С НЗП всё тоже самое, в начале запуска оно как маленький ребенок на извилистой горке, его состояние надо постоянно проверять и корректировать.
Для этого на предприятии и до внедрения ERP существовали инвентаризации. По складам и по НЗП на многих предприятиях – ежегодно, в конце года. Наверное, до ERP бывали и чаще, но я, честно, чаще без ERP не встречал, только если идет масштабная проверка какого-то конкретного подразделения.
В новых условиях, особенно на первом этапе, этого слишком мало – частоту и масштабы проверок придется увеличить и уточнить соответственно.
Серьезность задачи нельзя недооценить, поэтому рекомендую усилить группу, бюро или отдел внутреннего аудита как по численности, так и повышением их квалификации. Лучше, если произойдет добор кадров глубоко знакомых или с особенностями производств, или особенностями системы.
В любом случае, коллектив внутреннего аудита предприятия должен пройти обучение всему объему информации в системах, которые определяют качество и состояние НЗП. До них должна быть доведена логика процесса изменения НЗП в ERP, желательно с демонстрацией не только в учебных классах, но и на производстве.
Следующим шагом необходимо разработать и утвердить регламент и правила проверок, частота которых для каждого участка должна быть не реже раза в квартал, пусть даже выборочная инвентаризация или летучий контроль. К этой работе в обязательном порядке должны быть привлечены службы бухгалтерии и отдела, планирующего и контролирующего, пусть пока вручную, план производства, если такового нет, то диспетчерская служба предприятия, занимающая контролем состояния готовности изделий в производствах.
Регламент должен содержать не только периодичность проверок и указание на возможность «внеплановых проверок без предупреждения», но и:
- каким составом осуществляется непосредственно проверка:
- члены инвентаризационной комиссии;
- какие права она имеет;
- какую ответственность несет инвентаризационная комиссия, а какую проверяемая сторона, как во время проверки, так и в период без проверок;
- какие документы используются: при проверке; подтверждающие факт проверки; документы признания отклонений; документы списания в бухгалтерии и ERP; документы постановки на учет в бухгалтерии и в ERP;
- правила поощрения и наказания;
- механизмы поощрения и наказания.
Мне известны случаи, когда частота проверок каждого участка осуществлялась ежемесячно. Стоит оговориться, что ежемесячная сверка осуществляется не по всей номенклатуре, а только по дорогостоящим позициям и контрольным деталям, ОДНАКО – ежемесячно.
Не забываем, что номерные детали, независимо от наличия ERP, контролируются – в конце каждой смены, следовательно – ERP это тоже должна позволять.
ВАЖНО. В ряде случаев, особо запущенное состояние производства, ленивое сопротивления или саботаж со стороны руководства производств, имеет смысл не увеличивать число проверок и наказаний за недостоверность данных, а перехватить управление частью процесса.
В процессе достаточно точек перехвата управления, начиная от подтверждения и отпуска со складов ДСЕ извне, и заканчивая невозможностью начала транспортировки между любыми организационными единицами без подтверждения извне.
Ключевым моментом перехвата управления является ответ на вопрос – КТО возьмет на себя это самое перехваченное управление?
Хорошим вариантом решения данного вопроса является выделенная служба на базе службы внутреннего аудита или совсем новая структура, в которую вольется служба внутреннего аудита.
Альтернативным вариантом может стать служба, которая в последствие видится, как служба планирования и контроля плана производства на предприятии. Тогда, помимо перечисленных выше точек перехвата, можно отдать и функцию подтверждения сдачи изделия на склад готовой продукции.
Такая структура станет эффективной, если получит право подтверждения операций в системе, независимо и дублируя функции кладовщиц производства или сотрудников производства, отмечающих в ERP транспортные операции.
Это двойная работа, которая может снизить производительность обработки данных в систему, зато резко повысит качество операций и позволит системно снижать процент ошибок и откровенных подлогов.
Результат подпункта.
Разработан и утвержден регламент по ведению инвентаризации.
Выделена структура, которая проводит регулярные проверки.
Определены правила приведения в согласованное состояние физических остатков с данными ERP.
Определены правила выяснения и устранения причин возникновения нестыковок инвентаризации.
Создана отдельная структурная единица под задачи планирования производства на предприятии, которой поручен контроль движения ДСЕ по складам и между орг. единицами.
Запустить процесс совершенствования ДПЦ.

Сразу после запуска движения ДСЕ в ERP в системе начнет копиться информация по длительности циклов изготовления (ДПЦ) деталей и сборочных единиц, а также изделий в целом.
В ERP уже есть плановые данные по ДПЦ на каждую единицу ДСЕ, полученные через нормативные данные из PLM, а теперь появилась возможность сравнить их с фактическими значениями в ERP.
Какой бы теоретически идеальной ни была НСИ, я ещё ни разу не встречал предприятия, на котором, получив возможность сравнить нормативные данные ДПЦ с фактическими, инженерные службы и служба ИТ не были бы удивлены «таким большим несовпадениям».
Будьте морально готовы к тому, что расхождения по ДПЦ будут не менее чем у 60% деталей и сборок. Это обусловлено огромным числом факторов, для анализа которых потребовалась бы отдельная книга, поэтому просто примите как факт – у Вас это тоже случиться.
Прежде чем начать рассказ о том, каким способом устранять эти нестыковки, мы более внимательно посмотрим на ДПЦ изделия в целом.
ДПЦ всего изделия не равно сумме ДПЦ всех ДСЕ, входящих в это изделие.
Это связано с тем, что много деталей изготавливается параллельно и это вносит особенности в расчет ДПЦ изделия.
ДПЦ изделия приобретает смысл, только принимая значение максимального времени выполнения изделия, которое может быть рассчитано по самой длинной цепочке изготовления ДСЕ. Часто параллельность изготовления и особенности сборок таковы, что цепочка самого длинного цикла до получения результатов расчета не очевидна.
ВАЖНО. Цикл изготовления изделий считается на партию запуска, потому что его величина, в зависимости от объема партии изготовления будет меняться.
При наличии альтернативных маршрутов изготовления ряда ДСЕ, самых длинных циклов изготовления всего изделия становится несколько. К дальнейшему применению лучше брать самый максимальный цикл основного маршрута, даже при наличии более длинного альтернативного.
Почему вообще я уделяю вопросу цикла изготовления всего изделия отдельное внимание?
Довольно часто, на предприятиях, особенно где нет вообще ERP или какого-то аналитического аппарата, сталкиваешься с ситуациями, когда договора на изготовление изделий заключаются исходя из опыта работы в предыдущие периоды или по заданным свыше, без возможности поменять, параметрам отгрузки.
При этом, сроки сдачи этих изделий от даты подписания договора оказываются ближе даты сдачи изделия на СГП, согласно принятых циклов изготовления этих изделий при нулевых запасах.
Никто не обращает на это внимание просто из-за отсутствия информации по такому параметру как – цикл изготовления изделия. В итоге такие договора начинают закрывать из заделов на другие договора, сверхурочных, дозаказом части ДСЕ у других поставщиков и т.д. Всё это не только снижает чистую прибыль от реализации конкретно этого договора, а возможно и смежных, но и снижает уровень контроля качества, в частности по ДСЕ, заказанным на стороне.
Таким образом, данные по длительности цикла изготовления изделия при нулевых запасах должны в обязательном порядке стать настольным листом или экранной заставкой руководителей предприятия, сотрудников отдела продаж, закупок и подразделения, созданного для планирования деятельности предприятия.
Как Вы понимаете, искаженные значения ДПЦ каждой конкретной ДСЕ изделия вносят ошибки в конечное значение длины цикла изготовления изделия, а суммируясь, такие ошибки увеличивают величину отклонений и в итоге цикл изделия в ERP становится начисто оторванным от реальности.
Поэтому работам по выверке ДПЦ необходимо уделить очень серьезное внимание!
Самым качественным способом выверки ДПЦ является отработка и анализ выявленных отклонений по каждой операции каждого ДСЕ и по каждому перемещению детали, с проведением хронометража. Однако такой подход съест огромные временные и людские ресурсы.
Существует способ оптимизировать эту работу без серьезной потери в качестве ДПЦ.
Для начала мы должны принять для себя несколько постулатов:
- эталонным значением ДПЦ является достигнутое на реальном производстве, а не полученное через теоретические нормативные данные;
- в любом изделии есть детали, которые стоят на контроле, поскольку являются ключевыми для сборок и изделий в целом;
- главное сборки и только потом их компоненты.
Эти три постулата позволяют нам понять, что:
- начинать надо с конечной сборки, затем спускаться в выверке ДПЦ по сборкам ниже, пока не доберемся до деталей;
- изменения необходимо вносить в параметры НСИ в ERP и PLM, а не пытаться перестроить работу производств, под теоретические данные заложенных нормативов:
- выверку ДПЦ по деталям начинать надо с ключевых ДСЕ.
Важно то, что в любой момент выверки у нас есть контрольный показатель, который будет служить нам ориентиром приближения к верному значению или топтания на месте – длительность цикла изготовления изделия.
Это значение при нулевых запасах руководители в производствах знают и стараются их придерживаться в работе - плюс минус несколько дней. Такой точности нам более чем достаточно для оценки результатов выверки ДПЦ деталей и сборок.
После того, как работа по заведению информации в ERP о фактических ДПЦ деталей и сборок будет завершена – начнется этап оптимизации ДПЦ.
Вы можете сравнить нормативные значения, которые у вас были до начала выверки ДПЦ и текущие значения. Это сравнение покажет вам время отклонения по каждой ДСЕ и по изделию в целом.
Если эти отклонения будут в сторону сокращения цикла изготовления изделия, то это очень хороший результат, который сильно сократит Вам дальнейший объем работ, а возможно и вообще снимет вопрос оптимизации ДПЦ с повестки дня на данном этапе внедрения.
Однако, чаще всего результат оказывается обратным и цикл резко увеличивается. Столкнувшись с этим фактом, необходимо выявить отклонения и операции, вносящие максимальный вклад в отклонения – как правило, результат этого анализа подчиняется принципу Парето – в 20% ДСЕ кроется 80% отклонений ДПЦ.
С этими 20% Вам придется основательно повозиться непосредственно на рабочем месте. Этот процесс для себя я называю – походить за деталькой. Да – кому-то придется пройти её путь буквально неся её на руках, и не редки случаи, когда Вы будете вынуждены признать, что увеличение ДПЦ является объективным и верным.
При неправильном подходе процесс оптимизации ДПЦ может запустить задачу глобальной перевыверки НСИ. Постарайтесь следовать советам, данным выше и тогда, процесс станет проще, хотя всё равно будет длительным во времени.
Результат подпункта.
Процесс совершенствования ДПЦ запущен.
Следующая статья: Отступление 1. Без неё ERP на предприятии не внедрить
Автор: Андрей Лабутин