02.03.2019
Логика закупок - начало. Внедрение ERP на предприятий - шаг 5.
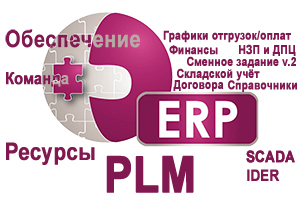
После внедрения этапов ERP, описанных ранее, возникает желание заняться автоматизацией планирования. Действительно, для начала работ в этом направлении в ERP уже всё есть, НО…
Ключевым вопросом для успешного внедрения планирования является качество информации. Ошибка в качестве исходной информации планированием множится и возводится в степень.
Поскольку внедрения PLM мы обеспечили предприятие и процессы качественным НСИ, теперь наступило время взять под контроль и управление ключевые процессы, от которых напрямую зависит срок и стоимость изготовления основной продукции предприятия. И начнем мы с:
- процесса обеспечения материалами;
- процесса изготовления ДСЕ и изделий.
Этой статьей начинается небольшой цикл материалов по автоматизации процесса закупок МКИ, который позволит ответить на вопрос – что и когда нам нужно, чтобы процесс изготовления не останавливался из-за дефицита материалов.
Предыдущая статья: Условия отгрузки и условия оплаты – почему это важно. ERP на предприятий - шаг 4.4.
Для упрощения описания процесса примем, что в течение года мы изготавливаем только одно изделие и отгружаем его разными партиями. Тогда теоретический процесс приобретения материалов будет выглядеть так:
- от партии продукции, через данные ERP (полученные из PLM) выбираются материалы, которые нужны для изготовления;
- норма этих материалов умножается на каждую партию изготовления и получается потребность в материалах на каждую партию изделия;
- у потребности на материал от срока отгрузки каждой парии обратной раскруткой цикла изготовления ДСЕ изделия, в которые входит материал, появляется дата отпуска в производство;
- возникает сводная потребность в материалах на каждую партию отгрузки изделия, со сроками поступления каждого материала на склад производства для отпуска под изготовление ДСЕ изделия;
- заключается новый договор на поставку материалов или создается заказ на закупку, который направляется поставщику на согласование в рамках уже действующих договоров закупок;
- осуществляется оплата аванса за материал;
- осуществляется поставка материала на предприятие;
- осуществляется окончательная оплата за поставленный материал;
- осуществляется перемещение материала на склад производства, изготавливающего конкретную ДСЕ изделия;
- осуществляется отпуск материала на изготовление ДСЕ;
- и так под каждую отгрузку.
Описанная последовательность не просто так названа – теоретической. Дело в том, что практически на каждом шагу этой классической модели возникают нюансы и отклонения, требующие прозрачности, информативности, подсказок от системы, а иногда и конструктивной управленческой реакции.
Сводная потребность в материалах.

Это уже очень похоже на бюджет материалов, но это ещё далеко не бюджет, поскольку мы ввели ограничение модели в одной изделие, и у нас не реализован подетальный план от плана производства и продаж.
Но посмотрите, сколько уже на этой стадии дополнительной информации нужно менеджеру по закупкам, чтобы провести качественное обеспечение МКИ производства:
- материал;
- изделие, в которое входит материал;
- количество отгружаемых изделий;
- периоды отгрузки;
- ДСЕ, на которые пойдет материал;
- норма материала на каждую ДСЕ;
- количество материала на каждую ДСЕ;
- подразделение изготовитель ДСЕ;
- склад подразделения изготовителя, куда надо положить материал;
- дата, до которой надо, чтобы материал оказался на конкретном материальном складе производства.
На данной стадии внедрения всю эту информацию менеджеры отдела закупок, после создания отчета, могли бы получать из ERP, но с этого момента реальная работа только начинается и автоматизацией этого процесса мы ещё не занимались.
Начнем с конца – от даты, когда материал будет отпускаться в производство.
Для менеджера по закупкам эта дата является лишь крайней датой, от которой он будет считать дату заказа материала. Существует такое понятие, как цикл закупок (ДЦЗ – длительность цикла закупок) – и это далеко не постоянная величина, которая складывается из времени выполнения следующих действий:
- оформление заказа поставщику;
- ответ поставщика;
- переговоры;
- оформление договора или подтверждение поставки под заказ по существующему договору;
- изготовление поставщиком партии материала нужного предприятию объема;
- доставка материала на предприятие;
- оприходование;
- входной контроль;
- обработка прихода на предприятии;
- перемещение материала на материальную кладовую подразделения.
Мы имеем огромный плюс – у нас есть данные последнего пункта перечисления, и не просто данные, а данные в идеальном состоянии – точная дата, когда материал должен оказаться на складе производства.
По всем остальным пунктам предстоит тяжелая работа, по созданию справочников, закреплению их за договородержателями на предприятии, заполнению и поддержании их в актуальном состоянии сотрудниками подразделений договородержателей.
Все перечисленные пункты, кроме изготовления материала и доставки, не зависят от поставщика, материала или изделия и могут быть жестко регламентированы на предприятии с указанием конкретных максимальных сроков обработки. Сроки по ним могут выглядеть так:
- оформление заказа поставщику (после обработки потребности) – 1 день;
- ответ поставщика – 3 дня;
- переговоры (уточнения по составу и количеству) – 5 дней;
- оформление договора или подтверждение поставки под заказ по существующему договору – 14 дней при новом договоре, 1 день при заказе в рамках существующего;
- оприходование – 1 день;
- входной контроль – 2 дня;
- обработка прихода на предприятии (оборот документов по службам предприятия) и подтверждение их в ERP – 1 день;
- перемещение материала на материальную кладовую подразделения – 3 дня.
Итого, по объективным и неизбежным работам мы уже получаем в максимуме – 30 дней с новым договором или 17 дней с работой в рамках существующего, которые надо добавить к дате перемещения на склад подразделения изготовителя.
ВАЖНО. В настоящей статье не рассматривается сам процесс и время прохождения процесса проведения тендера и выбора поставщика тендерной комиссией. Дело в том, что на каждом предприятии действуют свои регламентирующие процедуры по данному вопросу. В работах может участвовать неизвестное число служб с неизвестным числом согласовательных подписей. Всё это делает невозможным сколько-нибудь точное предположение о сроках проведения тендера, подходящих для любого предприятия. Отмечу лишь, что на практике такая процедура может занимать от 5 до 14 рабочих дней. Помните – это время также должно быть добавлено к времени цикла закупок.
Все перечисленные работы с днями могут быть заведены в один справочник единожды и будут изменяться крайне редко, только по факту выпуска новых регламентов на предприятии или вводу дополнительных работ в процесс закупки материалов.
Изготовление поставщиком партии материала.

На это требуется время, причем не просто время, а время, зависящее от:
- поставщика;
- материала;
- размера партии.
ВАЖНО. Стоит отметить, что этой величиной не стоит пренебрегать, поскольку с тех пор как США ввели санкции против России, в России появились позиции поставки, срок изготовления которых доходит до 8 месяцев.
На крупных предприятиях весьма распространенной практикой является объединение в одну партию одного и того же материала, заказываемого на разные изделия или в разные периоды. Да, это не очень хорошо сказывается на оборачиваемости, зато очень благоприятно на цене закупки.
У любого оптового поставщика, а тем более производителя есть понятия:
- минимальной партии – объем минимального заказа в единицах измерения материала;
- кратной партии – минимальный кратный прирост к объему партии.
При закупках менеджер вынужден придерживаться этих понятий и величин, именно поэтому довольно часто разные партии заказов одного материала объединяются в один заказ.
Чтобы менеджеры не держали эту информацию в голове необходимо завести в ERP дополнительный справочник по партиям отпуска, который будет связан с материалами и поставщиками.
ВАЖНО. По большому числу номенклатуры это время можно указать одинаковым, равным времени обработки и комплектования заказа для отправки заказчику – примерно 7 рабочих дней. Это допустимо для позиций, которые выпускаются огромными и партиями, не являются специализированными или закупаются со складов производителя или дилера.
Данные об объеме минимальной и кратной партии в справочник должны вводить менеджеры по закупкам. В тоже время, служба ИТ вполне может оказать им неоценимую услугу закачав первично данные по минимальной партии, и возможно даже по кратной партии, по всей закупаемой предприятием номенклатуре.
Правда, возможно это только, если вы уже ведете, хоть где-нибудь и хоть в каком-нибудь виде данные по закупкам хотя бы последние 3 года. Чем больше закупочных транзакций по каждому материалу с отдельным поставщиком вы имеете, тем более точную информацию может закачать в базу ИТ служба.
В предыдущих статьях по внедрению ERP, при внедрении сменного задания и складского учета, мы контролировали все поступления материалов с количеством, в том числе и на центральный склад предприятия.
Проблемой является то, что информацию от кого поступил материал, мы имеем только за последний год, по мере внедрения этапа ведения договорной деятельности.
В этих условиях ИТ служба может:
- сгруппировать все закупки по каждому материалу с одинаковым количеством, сохранив в списке только позиции, одинаковое количество в которых встречается не реже, чем в 50% закупок этого материала;
- пристыковать этот список к списку покупок за последний год, т.е. с уже собранными данными по поставщикам;
- положить в базу объемы c совпавшим количеством, которое закупалось наибольшее число раз, в привязке к материалу и поставщику. Положить в базу с какой-то отметкой о том, что это значение сгенерировано автоматически, чтобы менеджер знал, что значение подлежит проверке и уточнению;
- сделать отчет в системе, показывающий эти данные менеджерам по их номенклатуре;
- внести в ERP запрет на возможность выставления заказа на закупку для оплаты, пока в справочнике отсутствуют данные, хотя бы о минимальной партии заказа.
ВАЖНО. Один и тот же материал может закупаться у разных поставщиков и в разное время и одновременно (если основной поставщик не добирает объемов к нужному сроку). Это означает, что в справочнике один материал может фигурировать несколько раз с разной минимальной партией по разным поставщикам.
Параметр минимальной партии и кратной партии из ERP должны помогать менеджеру при формировании в ERP партии заказа подсказками:
- недобор до минимальной партии на объем - NN ед. изм.;
- количество превысило минимальную партию, но не кратно ни минимальной партии, ни кратной на NN ед. изм.;
- наилучший поставщик под заданный объем закупки – из списка поставщиков, по которым есть данные в базе ERP.
Объединяя разные потребности в одну партию, менеджер руководствуется не только данными о минимальной партии, но и одновременно решает задачи:
- обеспечения своевременности доставки;
- выхода на минимальную цену закупки за единицу материала;
- минимизации авансирования.
И если вопрос о предоставлении информации из ERP по сумме авансирования от конкретного поставщика решается довольно просто – выбором условий или графика оплаты из действующего договора или подсчетом процента аванса от суммы последнего заказа (альтернатива - минимальной суммы аванса среди всех заказов этому поставщику) при отсутствии действующего договора, ТО – данных по времени доставки взять пока просто неоткуда.
Время доставки материала на предприятие.
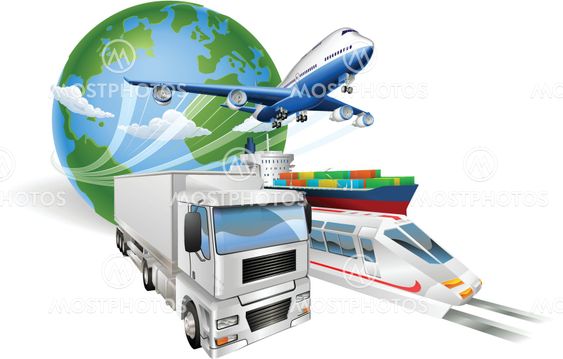
Так называемое транспортное плечо, выраженное в единицах времени. Эта величина зависит не только от местоположения складов отгрузки продукции поставщика, но и от способа доставки:
- ЖД;
- авто;
- авиа;
- море…
Каждый способ имеет своё время и свою цену, а доставка от одного поставщика может быть выполнена разными способами. Время доставки может быть довольно большим (особенно импортных позиций), кроме того, она может содержать ограничения на способы использования или вид транспорта, например: химия; кислоты; продукция, перевозимая в условиях микроклимата и т.д.
Информация о транспортировке также должна быть занесена в систему:
- поставщик;
- расстояние транспортировки, в км.
- материал;
- способ доставки;
- время доставки;
- цена за 1 км./т;
- особенности.
К сожалению, при заполнении этих справочников, ИТ служба может помочь только созданием интерфейсного окружения по их обслуживанию, потому что до решения о том, что такие данные в системе нужны, а заводить и сопровождать их будет служба закупок, информация об этих сроках содержалась только в бумаге и ни каким образом (кроме личных записей менеджеров по закупкам) не велась.
Полная стоимость закупки.
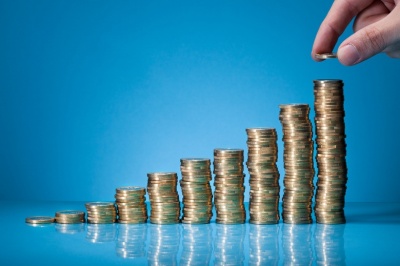
Из всего вышеперечисленного становится понятно, что стоимость закупаемого материала не есть стоимость закупки. Реальная стоимость закупки складывается из:
- стоимости закупаемой партии материала;
- стоимости работы всех сотрудников, участвующих в процессе закупки конкретной партии материала = сумма (средняя заработная плата сотрудника, деленная на произведение 22 рабочих дней и 8 часового рабочего дня и умноженная на время в часах, потраченное на работу по конкретному, договору, заказу и переговорам с поставщиком);
- стоимости транспортировки материала до склада предприятия;
- стоимости содержания и обслуживания материала на центральном складе = стоимость складского места в смену + стоимость работы по погрузке (разгрузке, перемещению по складу) + стоимость работ по входному контролю + стоимость работ кладовщиц.
Практически на всех промышленных предприятиях в стоимость закупки учитывают только стоимость материала и стоимость доставки, считая, что на фоне объемов закупок остальные значения будут настолько малы, что ими можно пренебречь. В тоже время на предприятиях довольно серьезно контролируют объемные и площадные показатели свободного и занятого места на складах. При этом вся заработная плата кладовщиц, комплектовщиц, закрепленных такелажников или грузчиков, менеджеров по закупкам складывается именно из перечисленных выше работ.
Когда мы заказываем партию чего-то на 100 млн. рублей, то только стоимость материала уже скрывает все остальные расходы, за исключением стоимости доставки, и то, если везём издалека или особыми условиями. Однако, при заказе, скажем, не дорогостоящих вспомогательных материалов или РЭН, как ни парадоксально, время на обработку одного заказа сильно возрастает, сложность выбора лучшего варианта тоже, а затраты на персонал или содержание на складе могут оказаться сопоставимы с затратами на материал и его транспортировку.
Подбор варианта.
После того, как вся вышеперечисленная информация будет занесена в ERP, система сможет выполнять за менеджера наиболее трудоёмкую функцию - подбора оптимального способа доставки продукции с:
- наиболее близким к необходимому сроком доставки;
- при минимальной цене доставки;
- и минимальном авансировании.
Необходимый срок доставки материала на предприятие считается от даты выдачи материала в производство за вычетом времени на выполнение внутренних процедур предприятия и может быть посчитан по формуле:
ДДМП = ДВМвП – К1 – РТК - ОЗП – ОП – Пе – ОД(ПП) – ПР – ВК – ОПП – ПММКП, где
- ДДМП – дата доставки материала на предприятие;
- ДВМвП – дата выдачи материала в производство;
- K1 – страховой коэффициент, на непредвиденные обстоятельства (можно принять 3 дня, дальше уточнять по факту);
- РТК – время выполнения тендерных процедур;
- ОЗП – оформление заказа поставщику;
- ОП – время на ответ поставщика;
- ПЕ – переговоры (уточнения по составу и количеству);
- ОД(ПП) – оформление договора или подтверждение поставки;
- ПР – оприходование;
- ВК – входной контроль;
- ОПП – обработка прихода на предприятии;
- ПММКП - перемещение материала на материальную кладовую подразделения.
Если вместо обозначений подставить принятые ранее значения этих параметров, то мы получаем максимальную дату доставки материала на предприятие:
- при наличии договора ДДМП = ДВМвП – РТК - 20 рабочих дней.
- при необходимости подписания нового договора ДДМП = ДВМвП – РТК - 33 рабочих дня.
ВАЖНО. Расчеты свидетельствуют о том, что в настоящее время крупным промышленным предприятиям в России очень сложно работать без запасов МКИ и заблаговременного заказа материала. Практику Just In Time в описанных выше условиях сегодня промышленности в России реализовать крайне сложно.
В ERP создается функционал, подобный следующему:
- находясь на определенной позиции списка материалов потребности, менеджер по закупкам может поменять автоматически сформировавшиеся объем к закупке (только увеличить) и дату прибытия материала на предприятие (только уменьшить);
- после чего нажимает кнопку «подбор поставщика» и в ERP происходит автоматический подбор поставщика под критерии: дата доставки меньше, но максимально близкая к дате прибытия материала на предприятие + минимальная цена доставки + минимальная сумма аванса;
- в результате подбора ERP выдает сеанс с двумя вкладками: на первой варианты с одинаковым числом дней доставки, ценой доставки, процентом аванса и способами доставки с указанием названия поставщика – все варианты подходят под критерии предыдущего пункта; на второй вкладке – все возможные варианты доставки со своими ценами и поставщиками;
- менеджер может выбрать любой вариант из вкладки 1 или выбрать вариант из вкладки 2, если критерий срока доставки из п. 2 не будет нарушен, а любой из двух оставшихся критериев станет лучше, чем в предложенных вариантах на вкладке 1, даже в ущерб другим критериям;
- менеджер выбирает подходящий под конкретную ситуацию вариант из предложенных и вся информация по поставке автоматически попадает в заказ на закупку.
Пункт 4 в данной последовательности просто необходим, поскольку на предприятии очень часто принимаются различные управленческие решения, которые могут пойти в разрез многим финансовым показателям, но однозначно обязаны не допустить срыва сроков поставки.
Если же управленческие решения будут связаны и со смещением сроков поставки, то менеджер обязан вернуться в сеанс списка материалов из потребности и указать в нужном варианте иную дату поставки материала на предприятие, после чего снова нажать «подбор варианта».
Следующий шаг – оплата аванса, здесь тоже не всё всегда бывает гладко…
Следующая статья: Оплачиваем закупку. Логика закупок при внедрении ERP на предприятии - шаг 5.1
Автор: Андрей Лабутин